How Image-To-Order Capture Provides Accountability For Outbound Fulfillment
How Image-To-Order Capture Provides Accountability For Outbound Fulfillment
StreamTech's Live Image Capture System Ensures Fulfillment Accuracy
How Image-To-Order Capture Provides Accountability For Outbound Fulfillment
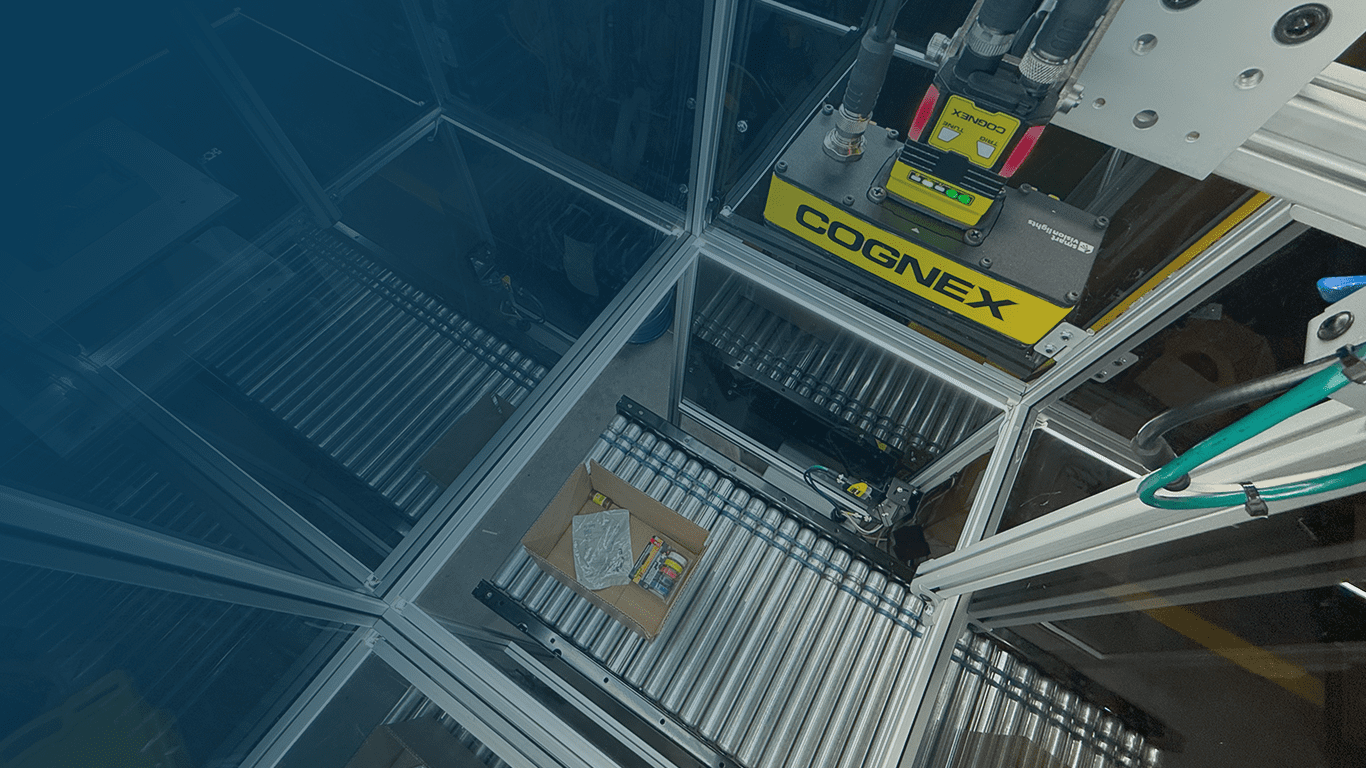
StreamTech's Live Image Capture System Ensures Fulfillment Accuracy
In warehouse fulfillment, regardless of whether the customer’s order contains car parts, jewelry, books, or medical instruments, order accuracy is the number one priority. Delivering an accurate order to every customer is the baseline for measuring success in fulfillment. It is the essential foundation upon which everything else is built. The second priority that follows closely behind accuracy is fulfillment speed. As operations ramp up with peak season or company growth, order accuracy becomes much more challenging because of the sheer volume of orders that need to be processed.
Any process involving human operators carries the risk of errors. This is the same with warehouse fulfillment operations. With manual fulfillment, orders could be picked incorrectly, contain an extra item, have the wrong label placed on the box, or be sorted to the wrong carrier.
Automation reduces errors by ensuring consistency and eliminating human mistakes. We rely on tracking orders and SKUs with unique barcodes. We track the progress of every order along the conveyor using induct verification scanners and perform parity checks at each stage of the fulfillment process. For engineered automation systems, we aim for over 99.5% accuracy, while attempting to operate at a high rate of speed (typically between 15 to 60 CPM).
Even with fulfillment automation, inaccuracies can still occur. Customers can still get the wrong items, or carriers can lose them in shipment. Without much recourse or proof other than scan data, warehouse leaders have a hard time proving they fulfilled the package accurately. But now, with unique vision camera systems we can.
Introducing StreamTech PackSight™ Camera Capture System:
StreamTech Engineering developed a camera vision system called PackSight™. The PackSight™ system does more than just capture images—it records high-resolution pictures of each completed order, whether open or sealed, as it moves along the conveyor. These images are then logged in a searchable database by the LPN (order ID).
Here are some ways this technology can enhance your operations:
Customer Service Insights: Provides data to customer service teams. In case of a complaint, operators can search the LPN database to verify whether an item was picked or not.
Carrier Accountability: Direct images of outgoing packages and contents help trace discrepancies to the carrier.
Internal Pick & Pack Auditing: Tracks accuracy in the pick and pack process using image capture and future machine vision capabilities.
Closed Box Imaging: Captures images at key stages like case sealer exit, label verification, and post-sort for damage claims.
Specifications:
- Acceptable image quality, 1.6 MP
- Single lens options, limited focus option
- White lighting solution
- Works well for both open box (pick audits) or sealed package (missing/damaged claims)
- Images are saved to a mass storage system and indexed by scanned barcode data
- Can perform binary package classification
Pairing The Image & Order Data: It’s More Than Just A Camera
You might ask, “Why not just use an IP camera to track my orders?” While a traditional camera can capture images of the items and shipping labels, the real challenge lies in organizing and tracking this data. For example, if you need to find an order labeled at 11:45 p.m. on January 3rd, you’d have to sift through hours of footage, which could include over 900 boxes if your operations runs at 15 cartons per minute. Searching through this footage wastes valuable time and effort. With PackSight™, that hassle disappears. Images are automatically linked to each order, allowing you to pull up the exact information you need in seconds. No more searching, no more guesswork.
The PackSight™ is a revolutionary system that offers more than just image capture. At StreamTech Engineering, we read the License Plate Numbers (LPNs) of each order, enabling precise tracking throughout the fulfillment process. As your order moves through each stage, the LPN is scanned and instantly communicated back to your Warehouse Management System (WMS). PackSight™ scans and logs each order by its unique LPN, giving you real-time images of open and closed cartons, as well as the shipping label details.
At StreamTech, we’re committed to enhancing efficiency and order accuracy in e-commerce fulfillment. We specialize in crafting tailored solutions that address core operational challenges, seamlessly integrating into your workflow. Through expert guidance and innovative engineering, we’ve helped countless businesses streamline their processes and improve both reliability and speed within their supply chains.
Ready to revolutionize your fulfillment process? Discover how PackSight™ can streamline your operations, improve accuracy, and elevate customer satisfaction.