The Last 100 Feet of Fulfillment, Fully Automated
Automating the end of line shipping and manifesting processes can deliver one of the greatest investment paybacks, with measurable impacts across a range of critical factors affecting warehouse operators today.
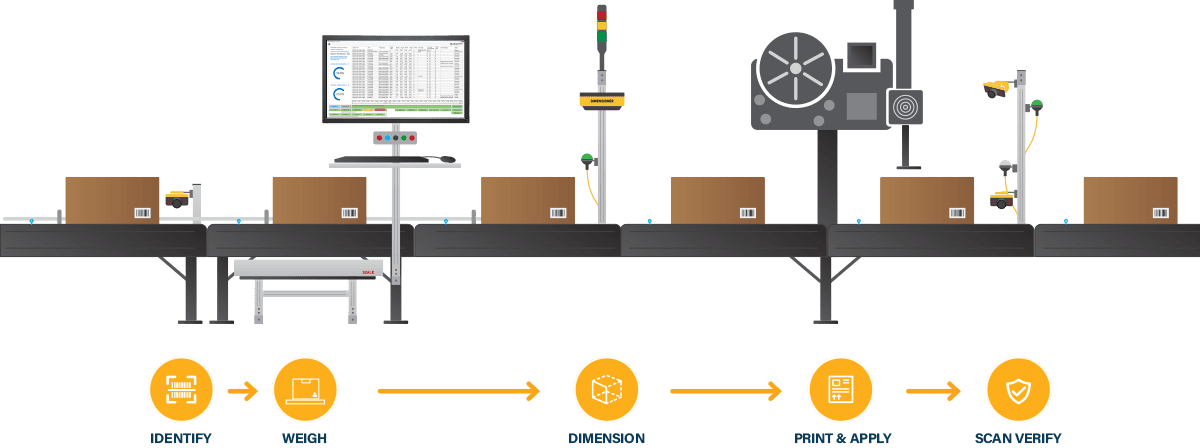
![]() |
Outsmart the Labor Shortage Remove manual hand scan, label, weigh and manifest of each shipment. Consolidate multiple manual pack and ship stations into a single lane so your staff can take up other responsibilities. |
![]() |
Control Carrier Costs Connecting the dim, weigh, scan, print apply systems with our WCS software to your WMS and multi-carrier allows real-time rate shopping between carriers, and prevents costly chargebacks. |
![]() |
Scale with Peaks and Growth Perhaps the most underrated benefit, scaling for weekly rush days and annual holiday peak is no longer as challenging. Automation also gives you room to grow without multiplying labor. |
![]() |
Accuracy Verification Multi-stage scan verification is critical to automating the fulfillment process. Removal of the random human error means increased customer satisfaction and fewer rates of return or loss. |
One Process, Many Configurations:
Sprinter™ Pre-Engineered
An all-in-one scan, weigh, dimension, print and apply shipping system
Sprinter™ can process approximately 600 to 1,000 cartons per hour, uses standard components, an accumulation conveyor for accommodating manifest response time, and is pre-engineered for fast installation. Sprinter™ is an excellent first step into automation.
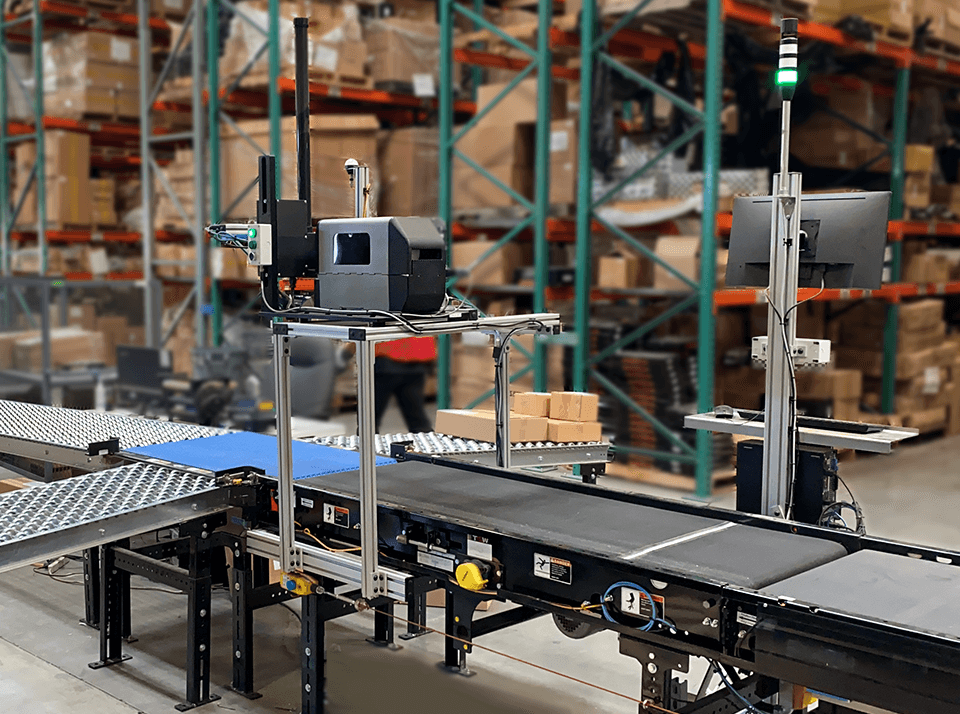
Sprinter™ Pre-Engineered
An all-in-one scan, weigh, dimension, print and apply shipping system
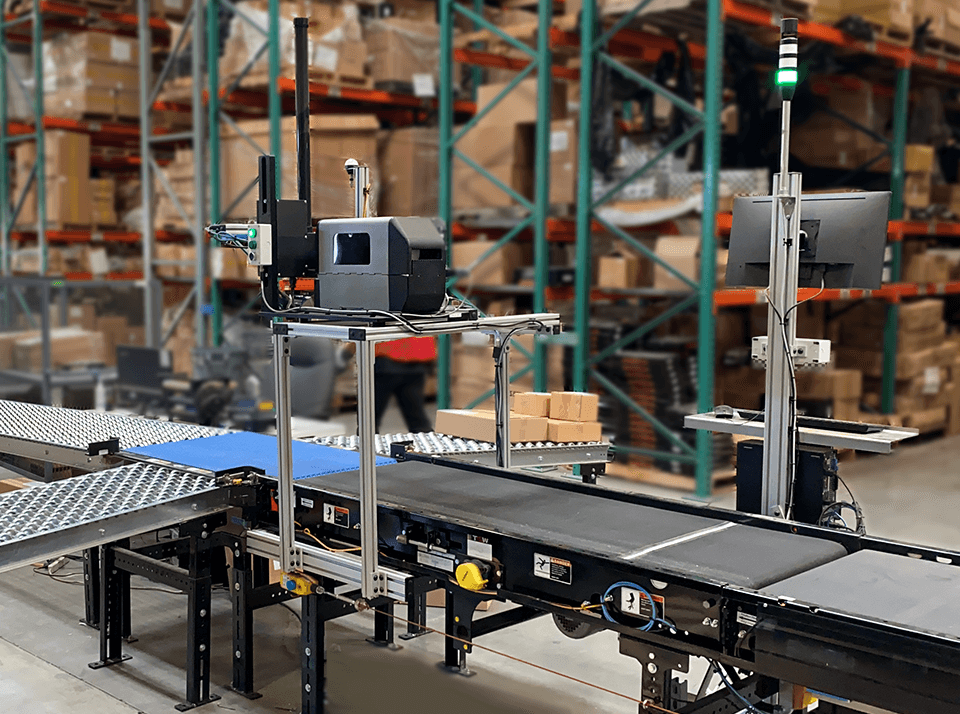
Sprinter™ can process approximately 600 to 1,000 cartons per hour, uses standard components, an accumulation conveyor for accommodating manifest response time, and is pre-engineered for fast installation. Sprinter™ is an excellent first step into automation.
In-Motion, Multi-Labeler
Higher speed scales, labelers in series enable increased throughput
Aggregated labelers in series allows for increased throughput, at approximately 20 cartons per minute, per labeler (e.g. 3 labelers achieves ~3,600 cartons per hour). Systems require tighter software manifest response time, and can be integrated with high-speed sortation.
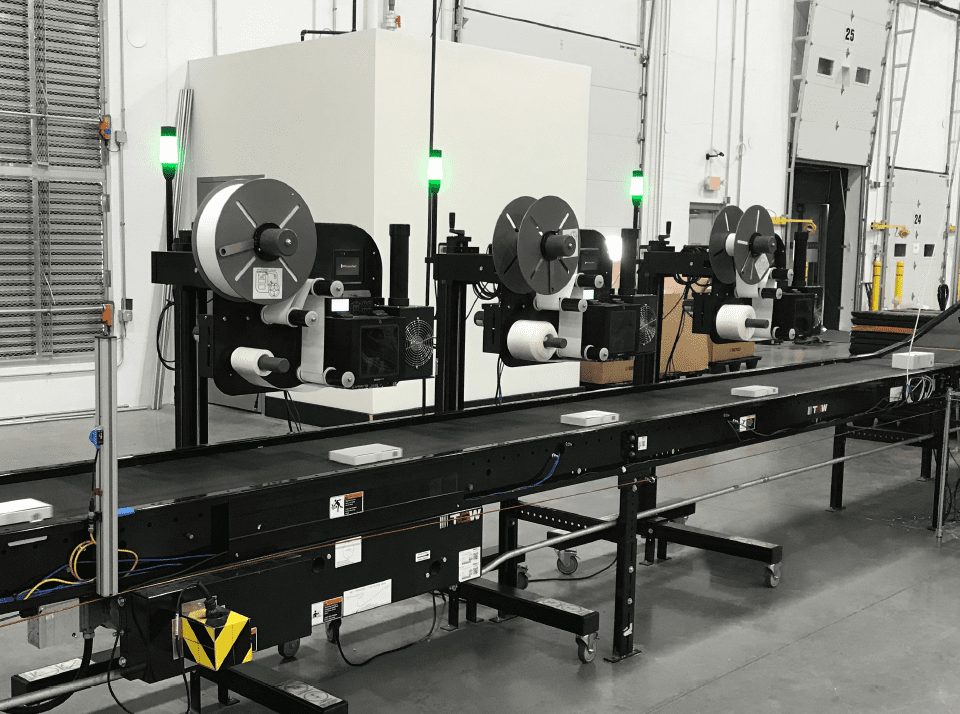
In-Motion, Multi-Labeler
Higher speed scales, labelers in series enable increased throughput
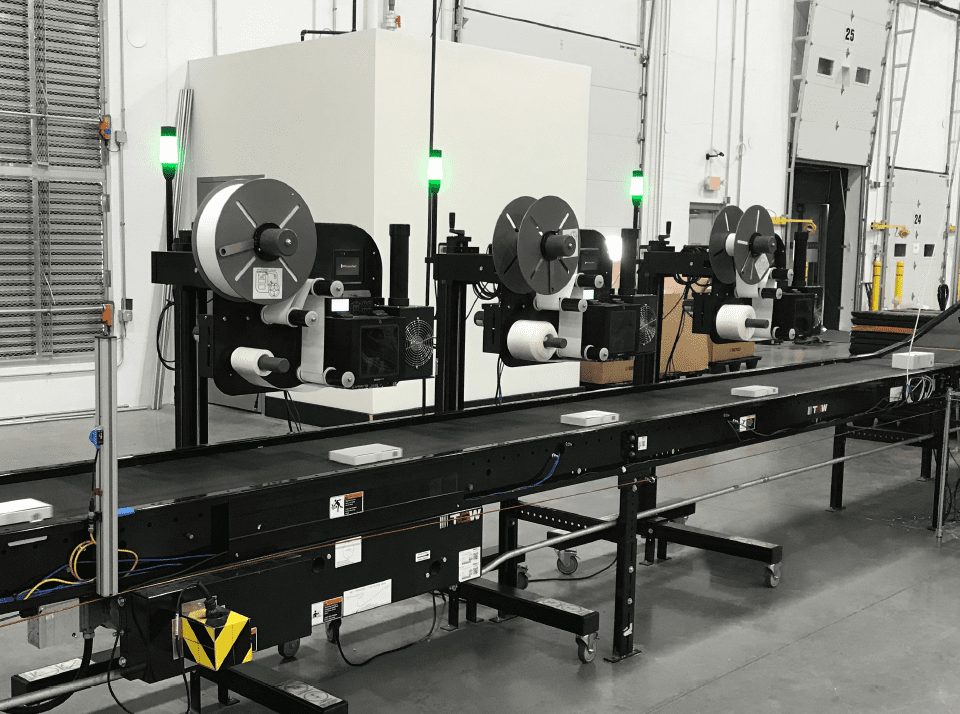
Aggregated labelers in series allows for increased throughput, at approximately 20 cartons per minute, per labeler (e.g. 3 labelers achieves ~3,600 cartons per hour). Systems require tighter software manifest response time, and can be integrated with high-speed sortation.
Multi-Line
Match your print-apply manifesting to discrete packaging equipment lines
Simplify systems by matching print-apply manifesting technology directly with discreet packaging technology. Each line can process approximately 20 cartons per minute (e.g. 6 lines shown achieves ~7,200 cartons per hour). Allows modular expansion.
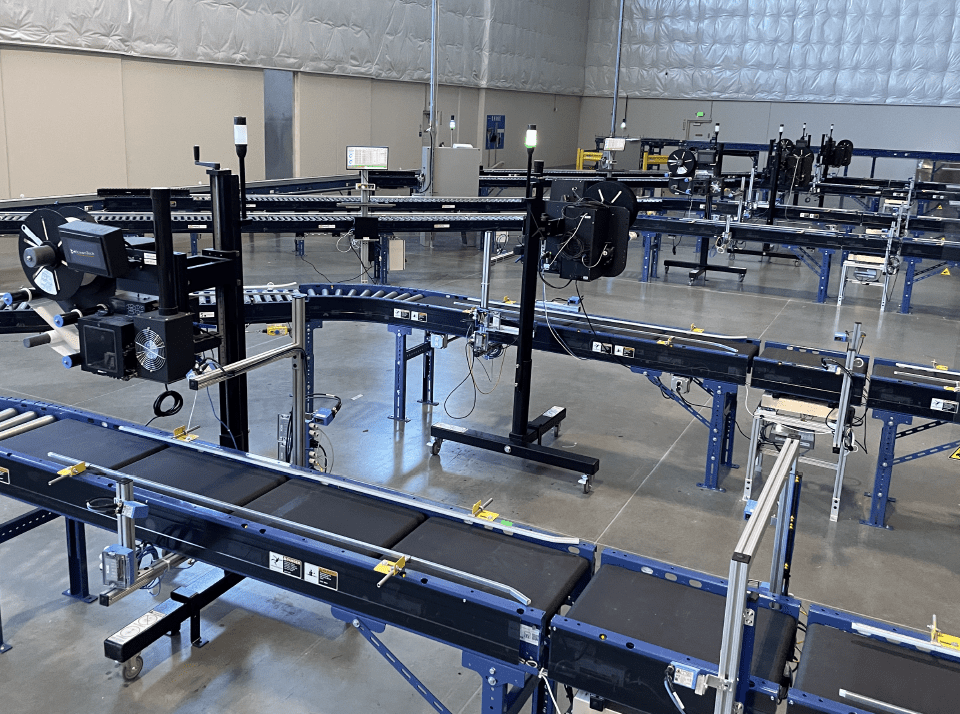
Multi-Line
Match your print-apply manifesting to discrete packaging equipment lines
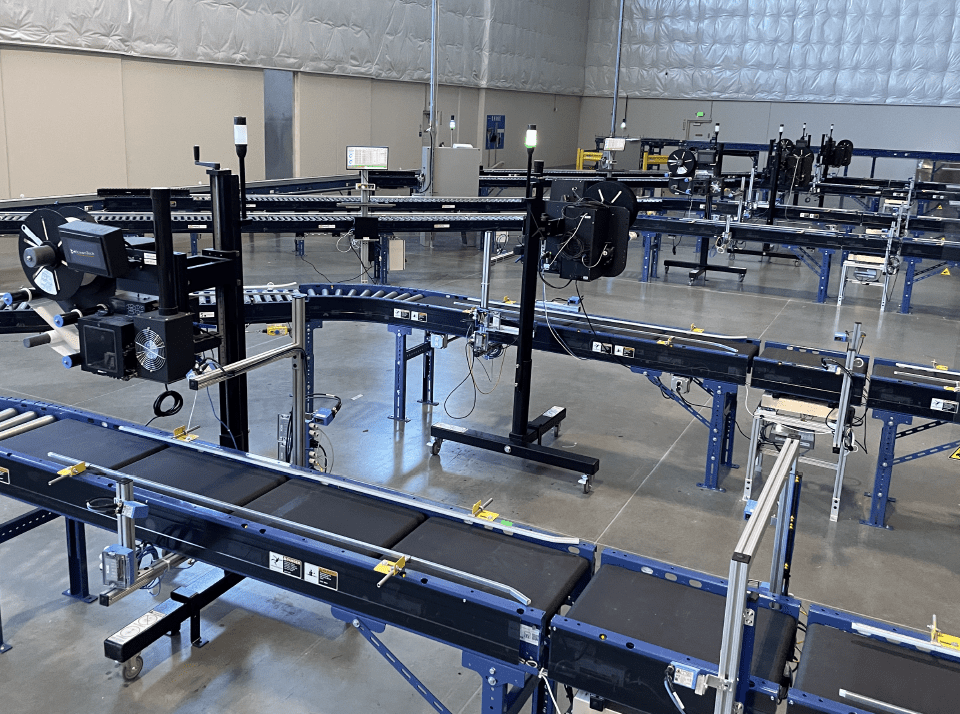
Simplify systems by matching print-apply manifesting technology directly with discreet packaging technology. Each line can process approximately 20 cartons per minute (e.g. 6 lines shown achieves ~7,200 cartons per hour). Allows modular expansion.
Helpful Articles:
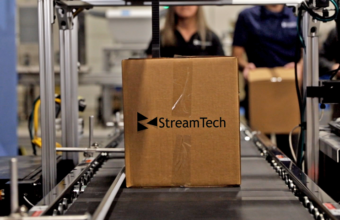
Sprinter™ Shipping System: Here's How It Works
The Sprinter™ is capable of scanning, weighing, dimensioning, print and applying and verifying. It can also integrate with a multitude of additional features. Ten feet doesn't seem like a significant impact, but by combining the individual process that are manually done you are not only saving space but time with an all-in-one system.
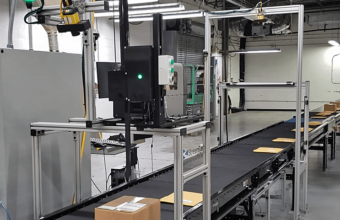
Why Choose Fulfillment Automation?
There are a lot of reasons for fulfillment automation, and it ultimately comes down to increasing operational efficiency. It’s not always just about speed. As you are considering the ROI (Return On Investment) for your next warehouse improvement project, here are a few of the reasons to consider fulfillment automation.
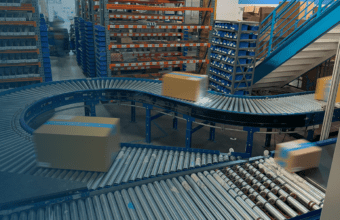
How to Calculate ROI for Warehouse Automation
Warehouse automation promises to not only streamline operations, but also to drastically improve efficiency and scalability. But the pressing question remains: Is the investment worth it? Return on Investment (ROI) is a key financial metric used to evaluate the efficiency of an investment or to compare the efficiencies of different investments. In the context of warehouse automation, ROI helps determine the financial return you can expect from investing in automation technologies compared to the cost of the investment. This calculation is essential in making informed decisions, as it provides a quantifiable measure of the potential benefits relative to the cost.