Common Shipping Errors: Problems & Solutions
As consumers continue to increase their online shopping habits, some going so far as to prefer it to retail shopping, it’s becoming more important than ever to have efficient shipping processes in place. Unfortunately, manual shipping processes lead to common shipping errors and increased costs due to human errors.
Fortunately, fulfillment automation offers a wide range of solutions to these challenges, assisting e-commerce businesses that want to streamline their shipping processes.
In this article, we’ll explore how businesses can use our shipping automation to optimize their processes to reduce shipping errors and associated costs.
Rate Shopping by Dimweight
According to a study of online retailers, 65% said that failed or late deliveries are a significant cost to their business.
Problem
Improperly priced and processed packages can harm a business’s bottom line by increasing expenses and potentially causing delivery delays. Inaccurately assessing the appropriate carrier information (such as weight and dimension) for a package can result in returned mail or back charges due, resulting in extra fees that accumulate rapidly, especially for large-scale shipping. Under-estimating weight or dimensions costs money in back charges from the carrier, and over-estimating them means you’re paying more than you need to.
As an example, say a business ships by weight and forgets to consider the dimensions of a package. For the purposes of the example, let’s say they sell custom body pillows. These products don’t weigh much, but they’re also quite long. Despite calculating the weight, carriers now charge by dimweight, dimensional weight, also known as volumetric weight.
In April 2022, the United States Postal Service introduced the USPS Nonstandard and Dimensional Non-Compliance fees to crack down on merchants who don’t put correct postage and those who ship parcels whose dimensional size affects their ability to ship as many parcels as possible. This change comes well after the 2015 changes UPS and FedEx made to recoup lost revenue.
If a package’s dimensions are not provided, you will be charged a fee of $1.50. If the dimensions are incorrect, it is a fee of 25 cents. Other carriers implement similar charges. While these charges may seem minimal, they can add up quickly if you ship out multiple orders.
To demonstrate how quickly these tiny charges can add up, say you ship out 7,000 packages per hour or 150,000 daily. If half of those packages incur carrier back charges and fees of $1.50, the total fee cost alone adds up to $112,500. Therefore, accuracy and dimweight are critically important.
Additionally, inadequate postage can lead to delays that can damage a company’s reputation and decrease customer satisfaction. Late or undelivered packages can result in missed opportunities, lost sales, and unsatisfied customers. In fact, according to PwC, in the United States, 17% of consumers will stop purchasing from a brand or company after one bad experience, and 59% will stop after several bad experiences.
Solution
Weight, dimensions, and accurate carrier and recipient information are required for a completely successful shipment. Relying on a person to manually weigh and measure the dimensions of each package will result in human error, which leads to carrier chargebacks. Additionally, some traditional dimensioning systems may not be capable of measuring irregularly shaped packages.
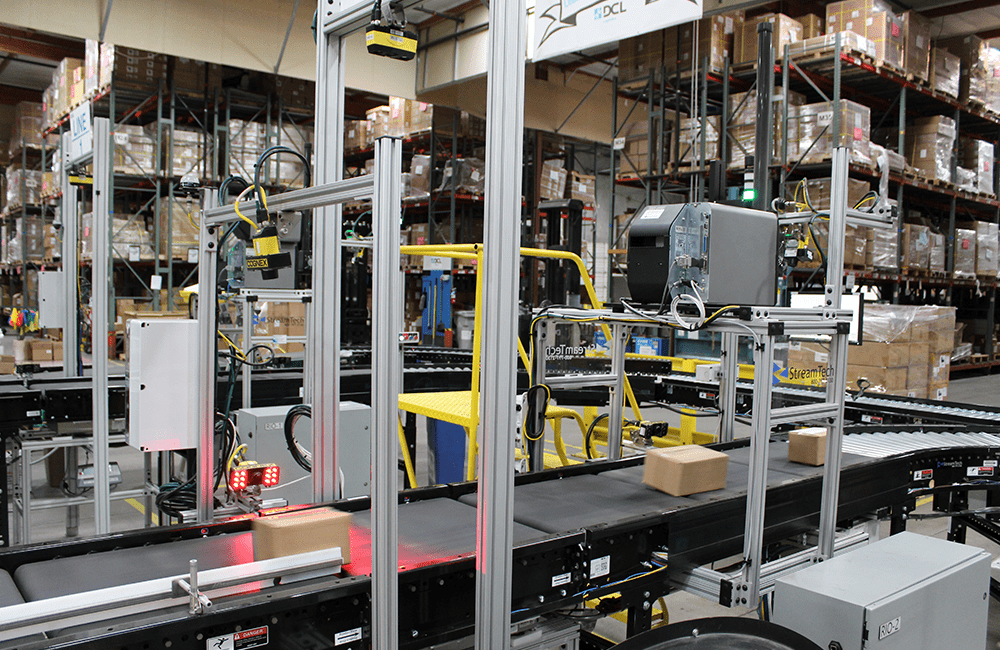
If this is your first foray into automating your warehouse or shipping center, considering an all-in-one scan, weigh, dimension, print, and apply shipping system is an easy way to reduce shipping errors due to incorrect postage.
These systems are often referred to as SLAM systems (Scan Label Apply Manifest), a term that was initially championed by Amazon during their push toward automating their fulfillment centers. SLAM systems are highly accurate, using scanners, order ID barcodes, and cameras with verification parity checking at every stage of the process. Orders only ship when the carrier label and LPN (License Plate Number, a unique order ID) information match, ensuring nearly 100% accuracy. This level of accuracy is actually of paramount importance for the automation to even run successfully.
SLAM systems such as StreamTech’s Sprinter™ calculate weight and dimension measurements simultaneously and with nearly 100% accuracy. Weight is captured along a conveyor scale. For dimensions, there are a few methods. Many dimensioners use LiDAR sensors and 3D imaging technology to capture a package’s length, width, and height. Others can capture dimensions using a light curtain that can be effective at calculating dimensions for longer packages. After aggregating the dimension and weight data, the system interfaces with your Warehouse Management System (WMS) or multi-carrier system to ensure the measurements correspond with the order, calculate carrier shipping costs based on the measurements, and print the postage label. Not only does this prevent accuracy errors, and help with label compliance, but it also improves efficiency.
Order Accuracy Verification
When a customer receives the wrong item, it is commonly due to an error in the picking stage. This could be due to two similar-looking items or an incorrectly stocked item.
23% of e-commerce returns are due to customers receiving the wrong item.
Problem
When a customer receives an item that differs from what they ordered or an incorrect quantity of items, it is a serious expense for your business. First, there is any possible fallout of the customer’s negative experience; this can be a negative review, the loss of future business, or, worse, both.
To protect your reputation, you may let the customer keep the incorrect item free of charge. This means you still need to pay for the replacement stock of the item you accidentally shipped out. This already affects your profit margin on this order. You also have to ensure the customer receives the correct item or number of items.
When you send the correct item or additional items to the customer, this incurs more operational costs. The entire pick, pack, and ship process starts over from scratch. This means you have to pay for the labor and materials it takes to ship the item, and chances are you’ll have to spend more on shipping costs to expedite it and keep the customer happy.
Not only that, but you also have to pay for restocking any items you incorrectly shipped out to ensure you have proper inventory levels – and double-check the quality of the returned item to avoid repeating the process if a damaged product is shipped to the next customer. For all of the above reasons, many retailers and 3PLs have opted to skip this process altogether and let customers keep incorrect items.
Solution
StreamTech offers a variety of different picking automation solutions to avoid mispicks and improve accuracy, all driven by the StreamTech WCS software.
One option to reduce shipping errors due to incorrect products or quantity of products is a pick-to-light system, which aids in manual picking by guiding employees to the proper aisle, SKU, and bin location, and helps them associate the proper items and quantities to the order they belong to. With this type of system, lights, colors, mini displays, and tablets can be used, and each pick is confirmed by the press of a button and can be verified throughout each step by the scan of any number of barcodes (either on the cart, aisle, bin, SKU, or order).
Other options may include voice-based or robotic-assisted picking, using a hybrid of these options to reduce human walking travel.
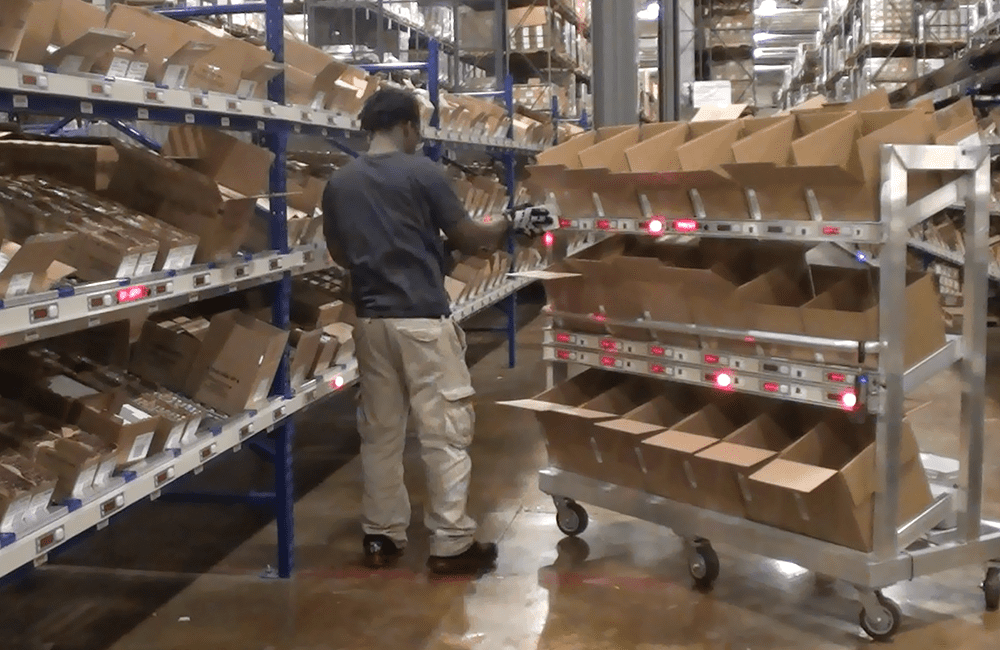
All of these systems are designed to improve picking accuracy and increase the speed at which your employees pick.
As a second quality assurance step, some warehouse operators employ a checkweigher, which can serve the dual purpose of capturing necessary weight data of each order, as well as verifying weight against a predetermined calculation of the order (this works if weights are already well documented for all SKUs in the WMS). During the picking and packing process, a checkweigher integrates with Warehouse Control System (WCS) software; as a package is weighed, the weight is sent to the WCS software to ensure it is within the acceptable range listed for each item in the order. If the package is too light or heavy, the checkweigher will alert you.
Using a checkweigher eliminates the risk of human error while increasing order accuracy, which in turn increases customer satisfaction.
Packaging Issues
When a customer receives a damaged product, it can have serious implications on your business. In fact, 20% of e-commerce returns are due to damaged products.
Problem
Improper packaging is one of the leading causes of customers receiving damaged products, which is costly for many businesses. Damaged products result in customer complaints and negative reviews, the potential loss of a repeating customer, as well as the costs to replace the product and ship it back out.
There are many reasons inadequate packaging can lead to a customer receiving a damaged product, including:
- Improper Dunnage (void fill): If the items are improperly protected, the order could arrive damaged. In many cases, adding dunnage is a very manual process with guesswork. Operators visually determine what looks right and tear off some dunnage. Sometimes operators may overfill and sometimes underfill. There are ways to automate void detection using sensors that dispense the appropriate amount each time.
- Poorly Constructed Packaging: Constructing RSCs by hand will result in human errors in sealing or assembling the flaps correctly. A wide range of carton erecting systems are available that will build trays (then lids) or custom-sized RSCs specifically designed for the items inside each order, with consistent results.
- Poorly Sealed Boxes: In the event that the flaps are sealed poorly, the box can pop open, and contents can spill out. In some cases, if a box is sealed poorly, the automated shipping label process can “seal” the box temporarily enough just to get through the automation, only for the contents to be lost later. StreamTech has employed a box closure technology to address this QA/QC issue prior to labeling for this exact reason.
- Improper Carton Selection: Many WMS software systems have what is called cartonization software built into them, which is the process by which the pickers know which carton is the best one to fit all the items in the order safely, efficiently, and for the best shipping rate. Poor carton selection can result in an excess void or overly dense containers that cannot support the items inside.
Solution
If employees are manually packaging products, it will inevitably introduce human error into the process. Additionally, if you already rely on fulfillment automation, the integrity of the box is vital to the success of your automated processes.
A variety of solutions can be employed to reduce shipping errors caused by packaging issues. In the case of a manually-constructed RSC, there are semi-automatic tapers and box erecting systems that can hold down and seal the bottom flaps while orders are packed and then allow the operator to push the box through to seal the top flaps. If the volume is higher and the ROI is justifiable, a wide range of on-demand carton erecting systems can be added to ensure a consistent, right-sized carton every time.
In fact, a carton erector can be a fantastic addition to end-of-line automation, as it provides a high level of assurance for the package’s integrity. For example, if you’re using a SLAM system, the box needs to be properly closed. Otherwise, it can lead to issues with the print-apply and dimensioning systems. In other words, the shipping label won’t properly adhere to the package, or the dimensional measurements will be incorrect. A package unable to be delivered for a missing label or incorrect dimensions results in hefty chargebacks from your carrier and a dissatisfied customer.
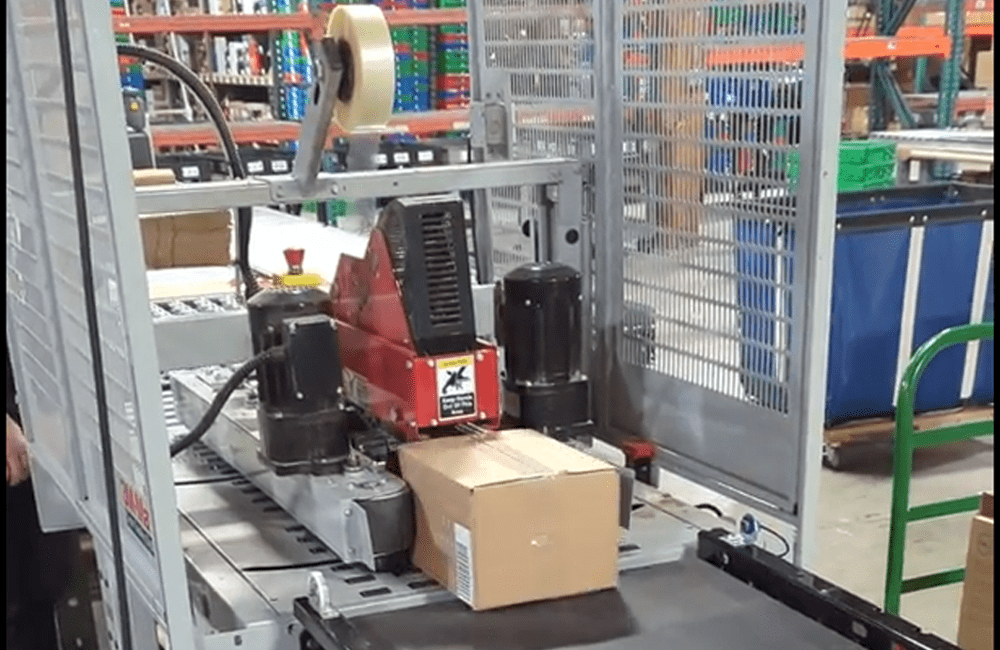
Additionally, a package that isn’t properly sealed can even result in damage to your labeling system, which is expensive to repair. It can also result in damage to the customer’s product inside.
In the case of poorly closed or assembled boxes, StreamTech can provide a package inspection system that acts as a QA/QC to ensure the box is constructed properly. This system can be incorporated directly after a box erector or a manual pack station, just before inducting packages into our Sprinter™ SLAM shipping system, which then dimensions, weighs, prints and applies shipping labels, verifies the process, and then can control sortation.
Wrong Address
Incorrect or incomplete addresses cause 74% of failed deliveries.
Problem
Incorrect shipping addresses can impact businesses, increasing costs and customer dissatisfaction. When products are shipped to the wrong address, a business may incur additional shipping fees and labor costs to reship the product to the correct address or deal with the fallout of the customer not receiving their order. These costs can quickly add up and impact the bottom line. Moreover, incorrect shipping addresses can delay delivery, leading to negative customer reviews and harming the business’ reputation.
Solution
Automating your shipping using StreamTech’s Sprinter™ Shipping Station is a simple way to reduce shipping errors due to wrong addresses because it has a deep connection to your order database and it has verification built-in.
The Sprinter relies on a tight connection to your TMS (Transportation Management System) software, or multi-carrier software. This connection allows us to gather the data of the package, transmit that data, and receive the shipping label associated with that order. The system scans the LPN or identification barcode at the beginning of the process, records dimensions and weights, and then applies the shipping label it receives from your TMS. After applying that label, there is a verification scan that takes place, along with a parity check.
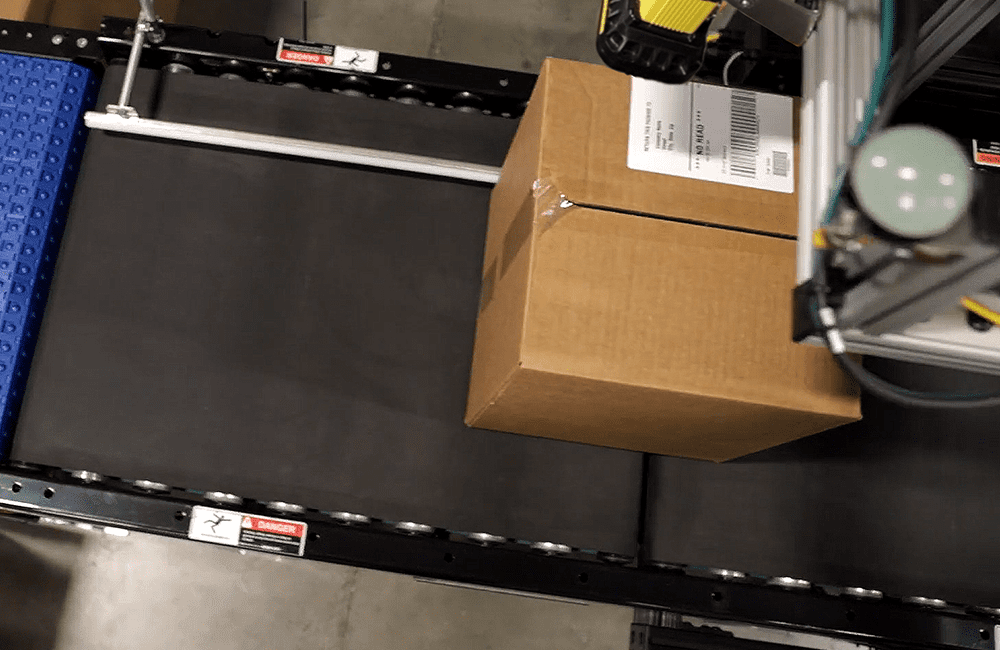
During the parity check, the WCS ensures that the shipping label is correct and that it matches the order associated with the LPN that it’s supposed to.
By leveraging our Sprinter™ Shipping Station, businesses can improve shipping accuracy and efficiency while minimizing the impact incorrect addresses have on their bottom line.
Conclusion
Implementing fulfillment automation is a simple and effective way to reduce shipping errors and their costly consequences.
If you’re ready for automation, contact us today.