Print & Apply Shipping Automation
Full scale print and apply, dimensions, weighing, manifesting systems
Beat the Monday Rush, While Reducing Costs
The Last 100 Feet of Fulfillment, Fully Automated
Automating the end of line shipping and manifesting processes can deliver one of the greatest investment paybacks, with measurable impacts across a range of critical factors affecting warehouse operators today.
Why Automate the End-of-Line?
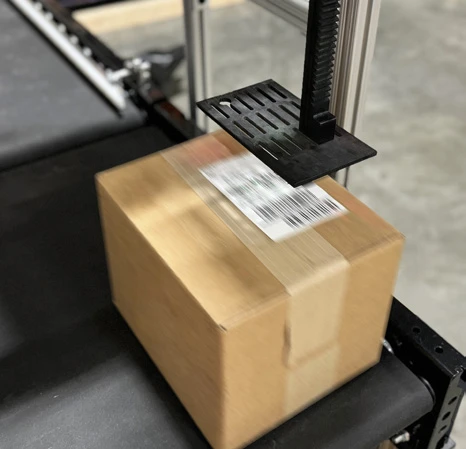
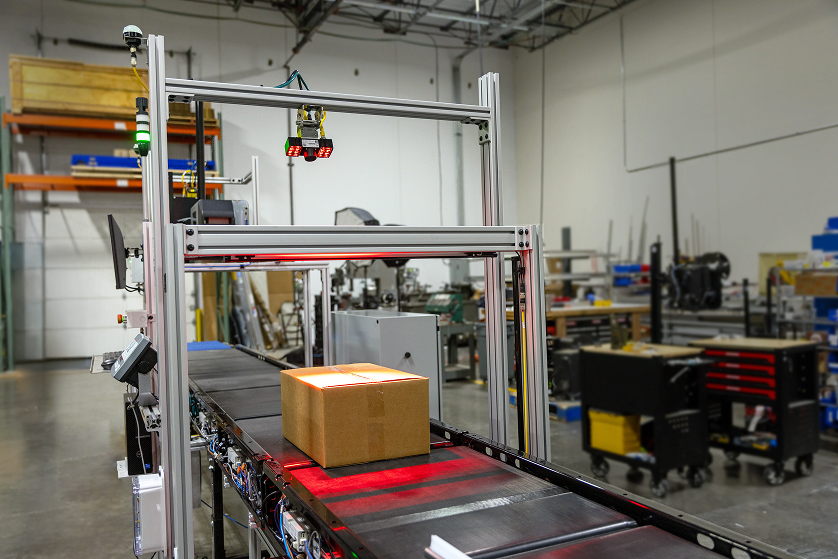
Control Carrier Costs
Connecting the dim, weigh, scan, print apply systems with our WCS software to your WMS and multi-carrier allows real-time rate shopping between carriers, and prevents costly chargebacks.
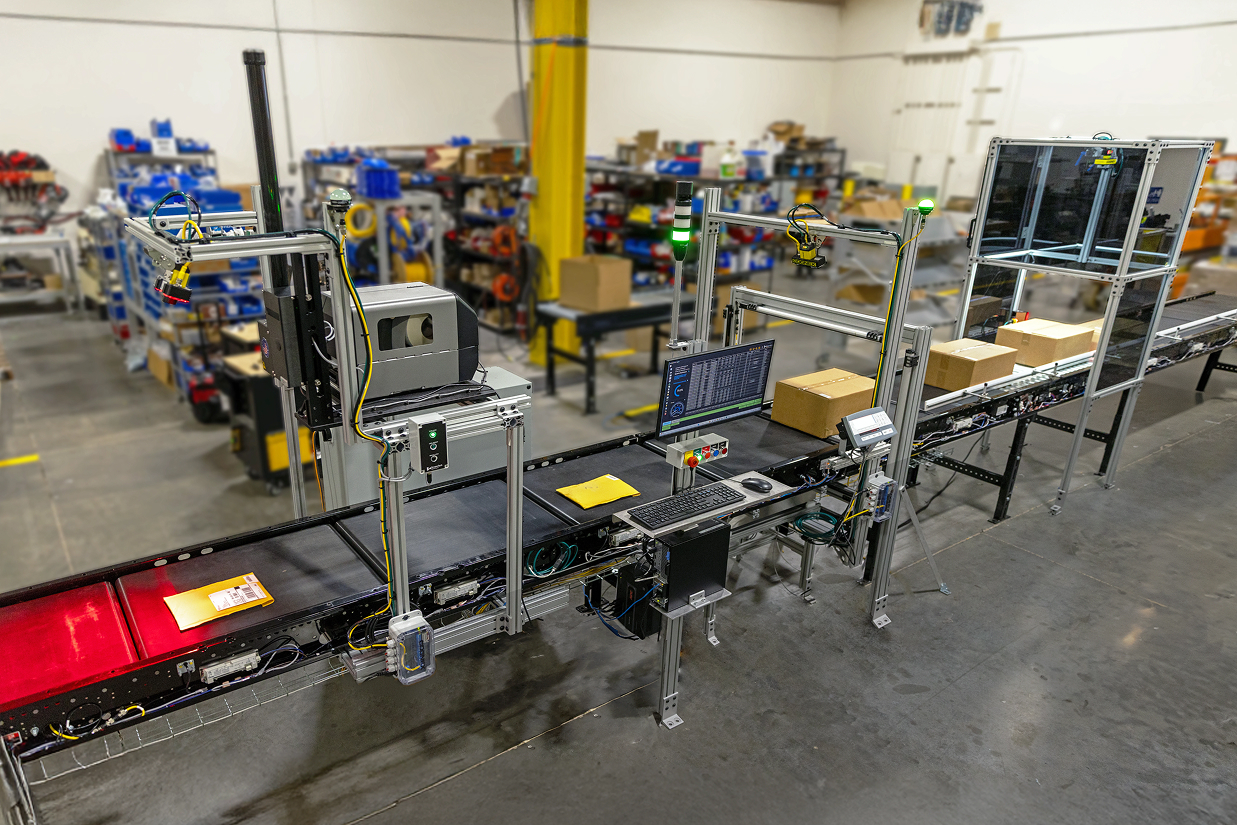
Scale with Peaks and Growth
Perhaps the most underrated benefit, scaling for weekly rush days and annual holiday peak is no longer as challenging. Automation also gives you room to grow without multiplying labor.
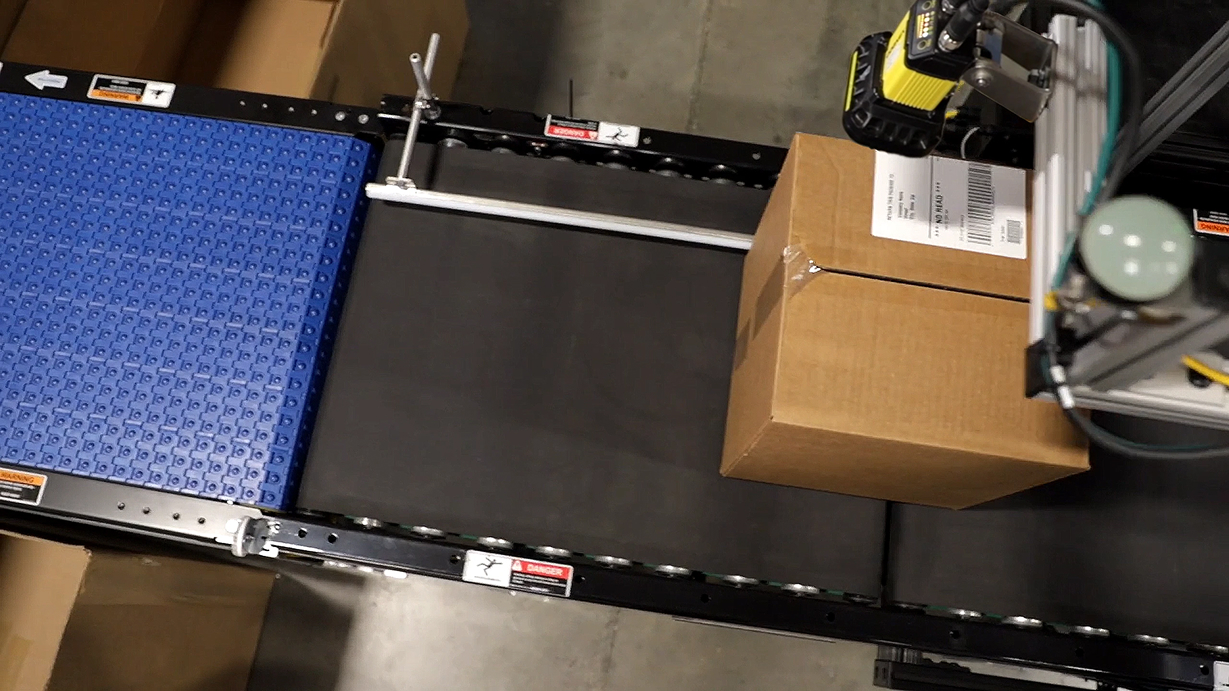
Verify Order Accuracy
Multi-stage scan verification is critical to automating the fulfillment process. Removal of the random human error means increased customer satisfaction and fewer rates of return or loss.
Here’s How Automated Print & Apply Works
Our print and apply systems are designed to ensure every package moves through your operation with precision and efficiency. It all starts with accurate identification of the barcode on the package. Next, camera-based systems capture exact package dimensions to prevent carrier overcharges and drive accurate labeling and sortation.
Once identified and measured, each package is weighed using high-throughput, high-accuracy scales, with optional checkweighing to compare measured and expected weights for quality verification. Finally, scan verification ensures that the applied labels and LPN barcodes match, exceptions are managed seamlessly, and the entire process integrates with downstream functions like sortation for fast, reliable throughput.
Our Products
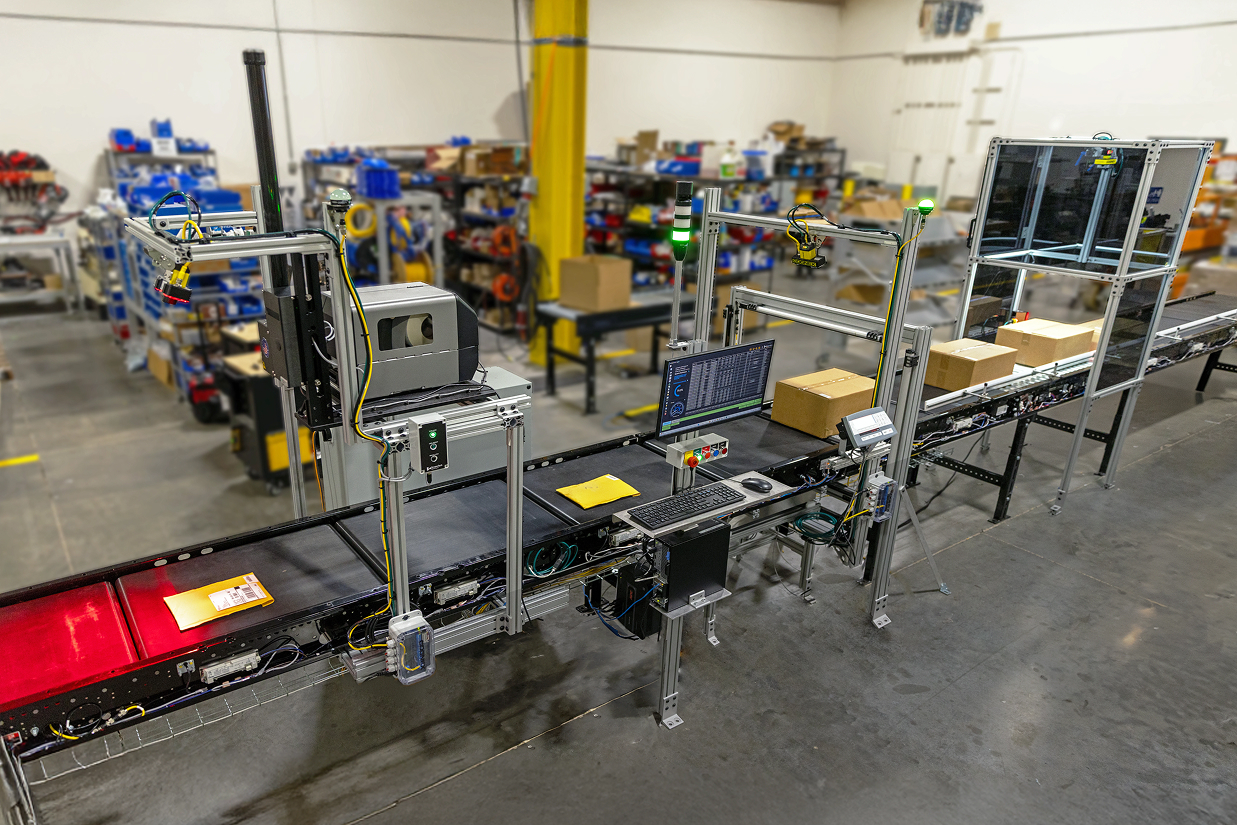
Sprinter™ Pre-Engineered Fully Automated Shipping System
An all-in-one scan, weigh, dimension, print and apply shipping system.
The Sprinter™ can process approximately 600 to 1,000 cartons per hour, uses standard components, an accumulation conveyor for accommodating manifest response time, and is pre-engineered for fast installation. It is an excellent first step into automation.
Spark™: Compact Pack & Ship System for Smaller Volume Shippers
Automate weighing, dimensioning, labeling, and verifying — right at your pack table.
The Spark™ is a small plug-and-play semi-automated shipping system designed to streamline the final steps of order fulfillment. Positioned next to your existing pack table, Spark™ can scan, weigh, dimension, label, and verify in one compact footprint. Simply scan the packing slip, close the box, and Spark™ does the rest.
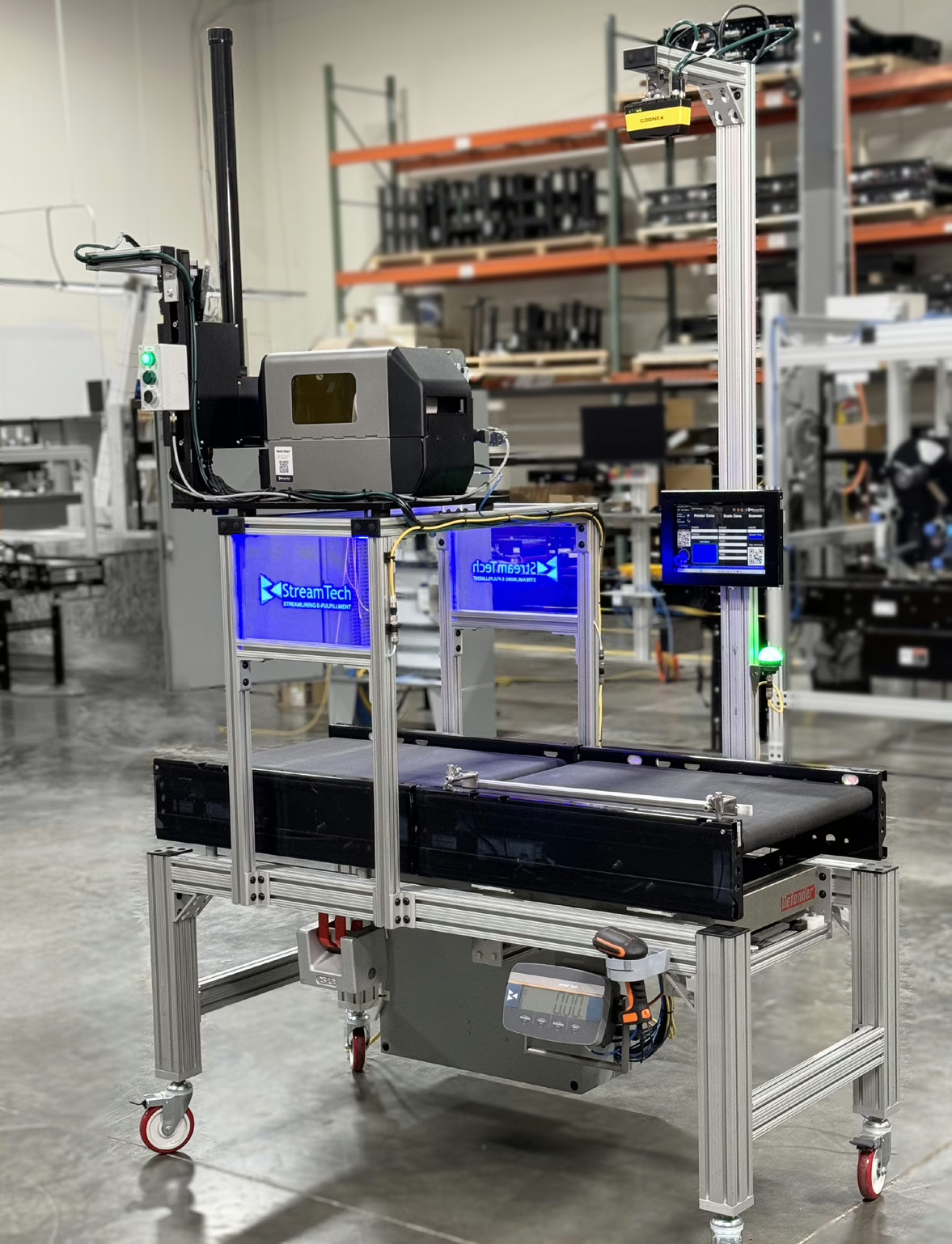
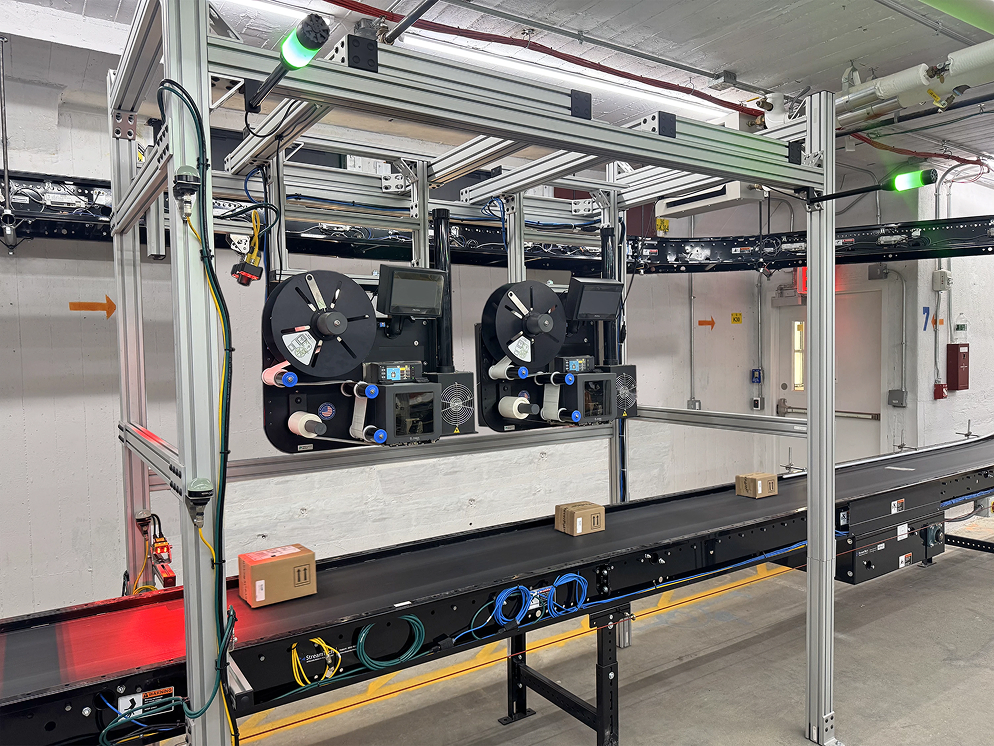
High Speed In-Motion Shipping Systems
Faster scales, labelers in series increase the throughput of the system.
Aggregated labelers in series allows for increased throughput, at approximately 20 cartons per minute, per labeler (e.g. 3 labelers achieves ~3,600 cartons per hour). Systems require tighter software manifest response time, and can be integrated with high-speed sortation.
Driven by Intelligent WCS Software
Intelligent Warehouse Control System (WCS) Software
StreamTech bundles our operational and maintenance know-how in the onboard WCS software app that comes on the included system (Windows) PC, with rich functionality that supports troubleshooting and enhances uptime. The intelligent warehouse control (WCS) software easily integrates with rules-based multi-carrier systems or direct carrier interfaces.
- Extensive troubleshooting built-in to the system
- Smart filtering of label files
- Expandable for growing customers
- Rich scan, production, and maintenance statistics with configurable retention
- Backup UPS included protecting PC and SQL database
- Multi-level security, multi-user login
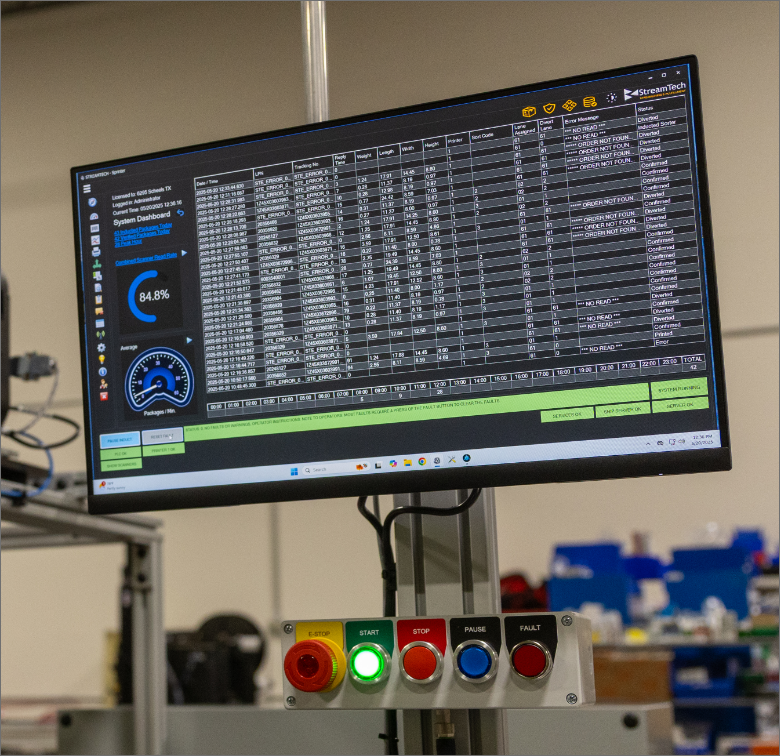
Other Labeling Solutions
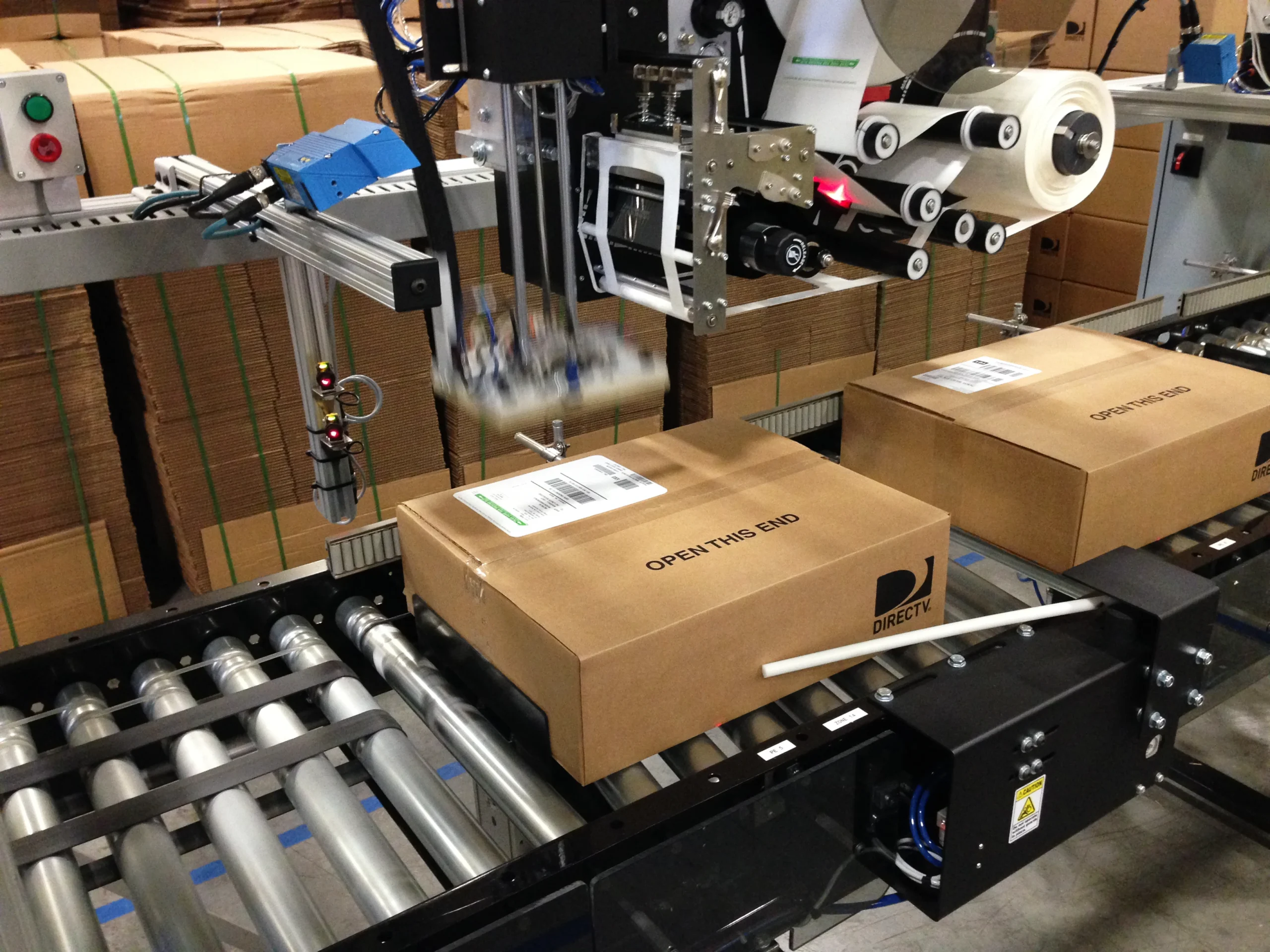
DuplexPackSlip Labeling
Add a packing slip and/or return label to orders which ship in their original packaging. DuplexPackSlip® uses a special double-sided label which allows the top portion to be peeled to reveal a hidden pack slip, return label or other message on back. It can also be used in triplex with a label below. Now available in an environmentally-friendly linerless configuration.
Robotic Labeling Technology
StreamTech has developed a robotic arm that can be pre- programmed for a variety of labeling recipes. The system can peel a label from a printer, and apply it on any side of the box, in virtually any configuration, including wrapping over the edges.
We also use dimensioning systems to calculate the skew of the package. This robotic labeling system can be a good tool for complex applications where requirements can vary regularly.
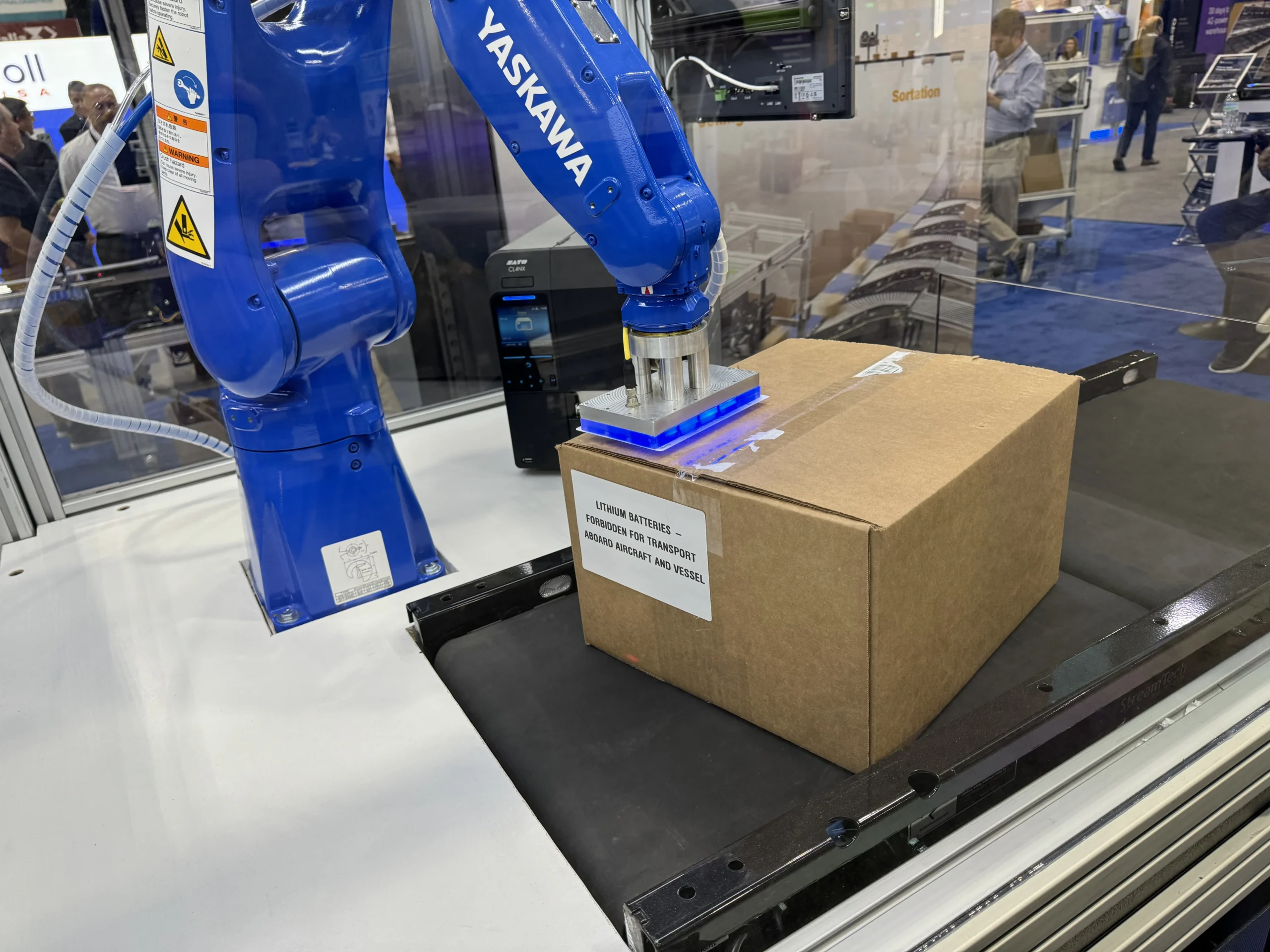
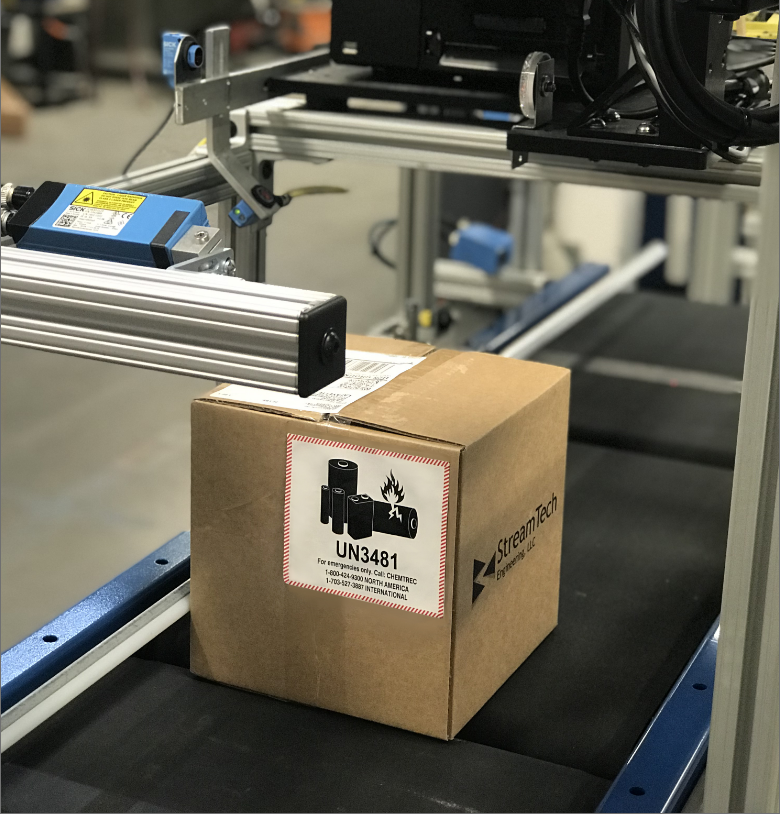
Compliance, Hazmat Labeling
Shipments containing batteries or other hazardous materials must be labeled for DOT compliance, with specific size and data required. Automate UCC and other compliance requirements while accounting for shipping quantities with print and apply technology.
What our customers say
Frequently Asked Questions
If you have any further questions, please reach out to us and we will be glad to help.
What processes can be automated with a print & apply system?
StreamTech’s print & apply systems automate key end-of-line tasks including package identification, weighing, dimensioning, rate shopping, shipping label application, and label verification—removing the need for manual handling and reducing fulfillment errors.
How do automation systems help reduce shipping costs?
By capturing accurate weight and dimension data in real time, the system ensures proper rate shopping between carriers and prevents chargebacks due to incorrect dimweight. Automation also improves label accuracy and lowers labor costs by consolidating manual ship stations.
Can these shipping automation systems handle high-volume or peak periods?
Absolutely. Systems like the Sprinter™ can process 600–1,000 cartons per hour, while in-motion systems using multiple labelers can reach over 3,000 cartons per hour. These solutions are designed to scale with growth and meet the demands of weekly or seasonal peaks.
What if we don’t have space for a full shipping automation system?
StreamTech offers compact solutions like the Spark, which delivers scan, weigh, dimension, label, and verify functionality in a plug-and-play unit next to your existing pack table—making automation accessible without major layout changes.
Yes. The DuplexPackSlip® system prints a double-sided shipping label that peels to reveal an internal pack slip, return label, or customer message. It’s ideal for original packaging shipments and now available in linerless formats for added sustainability.
Featured Articles
-
Best Practices
Why the Best Material Handling Solutions Begin with the Right Questions
In today’s high-pressure fulfillment world, it’s tempting to “just get a quote” and keep things moving. But when it comes to automation, fast answers…
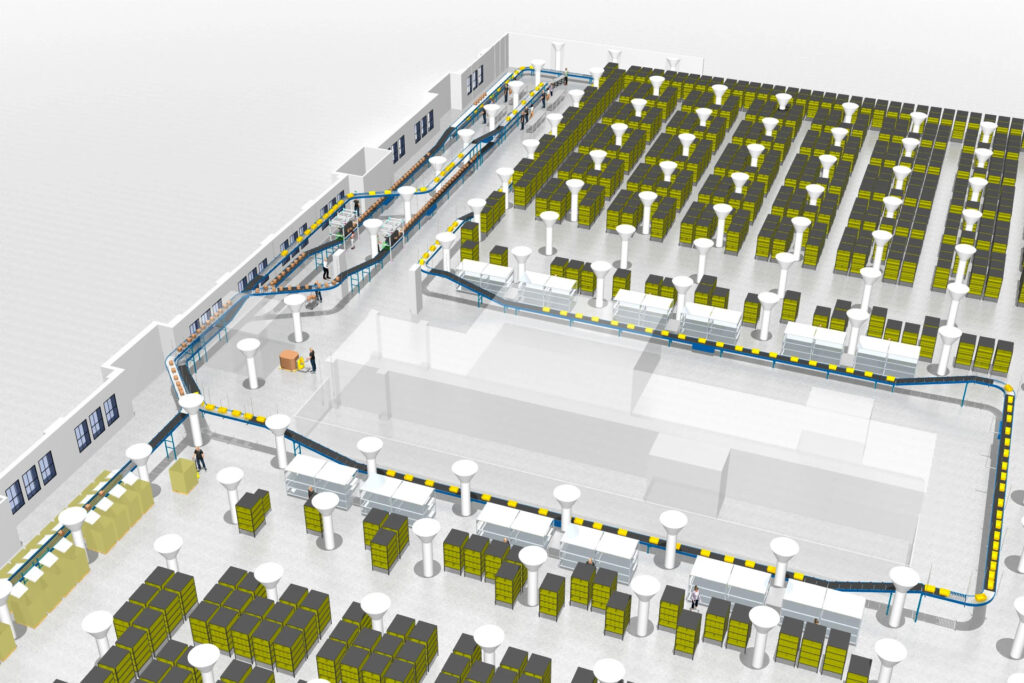
Ready for Automation?
Share your fulfillment challenge with us and we’ll design a custom solution for your business before you sign a contract
"*" indicates required fields