VelocityPick™ Pick-to-Light
Light Directed Picking Systems
Speed. Accuracy. Simplicity.
Simplify Order Picking with VelocityPick™
Our VelocityPick™ pick-to-light system simplifies picking by using light-guided technology to direct pickers to the correct bin, while also displaying the required quantity. This eliminates the need to memorize locations and makes it easy to scale your product offerings without adding complexity to the pick process.
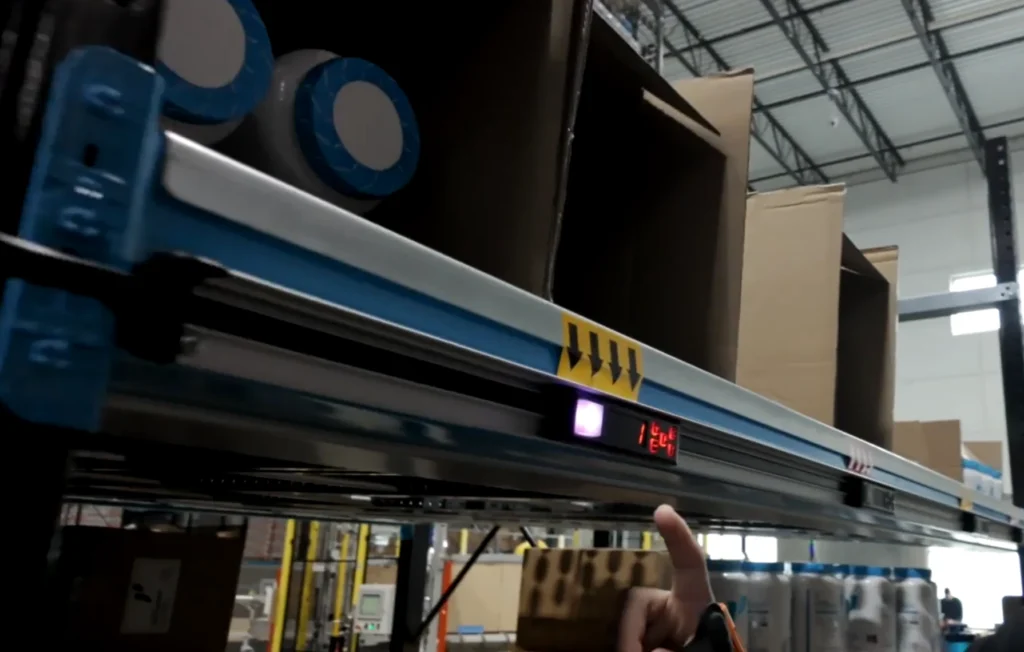
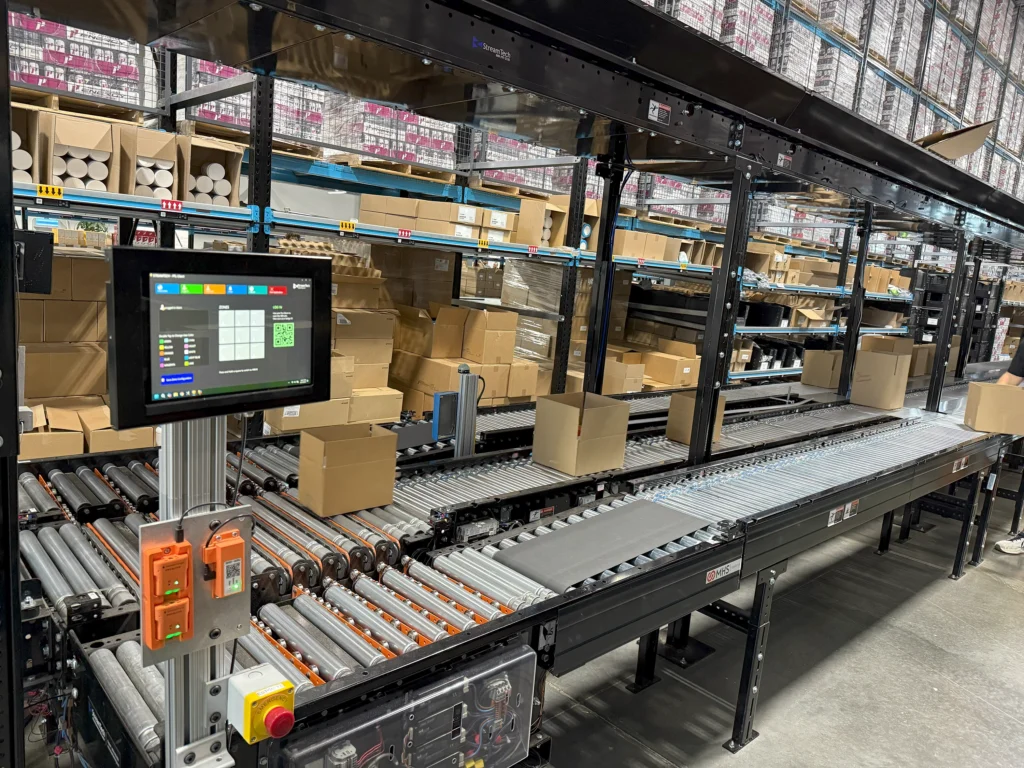
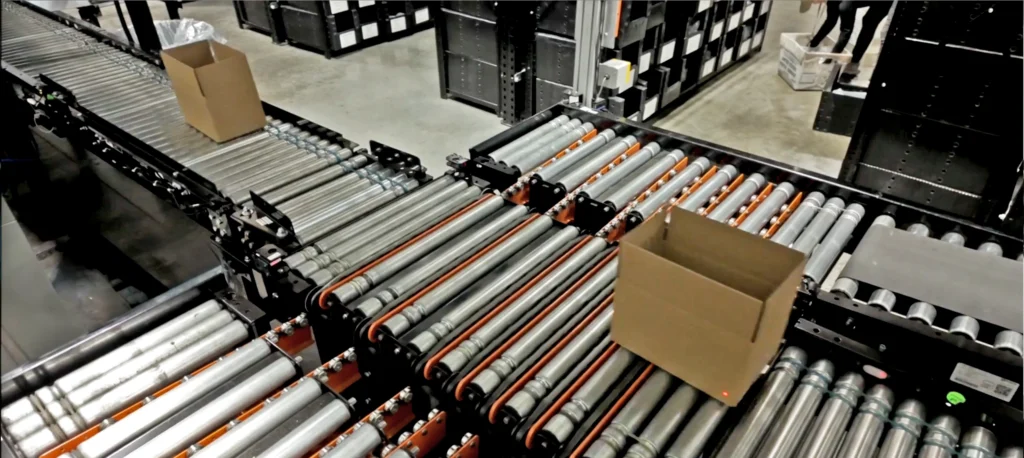
Benefits of Pick-to-Light
Increased Throughput
Pick modules are designed to optimize the picking process by organizing inventory in a systematic manner, resulting in faster order fulfillment and increased throughput as orders convey through the pick zone.
Real-Time Inventory Accuracy
Real-time visibility into inventory levels ensures better stock control, reducing stockouts and overstock situations. This leads to more accurate demand forecasting and efficient replenishment, lowering overall inventory costs.
Enables SKU Flexibility
By simplifying the pick process, guiding your employees to the correct SKU and quantity, this greatly reduces the training time necessary. It also enables the business to increase SKUs, add new products, without increasing pick complexity.
Scalable & Flexible
Solutions
Pick modules can be designed and configured to adapt to changing business needs and inventory profiles. Whether accommodating seasonal fluctuations, new product lines, or shifts in demand patterns, pick modules offer scalability and flexibility to support evolving warehouse operations.
Reduced Errors
With a structured layout and clear labeling systems, pick modules minimize the likelihood of picking errors. Pick modules help to prevent mistakes such as picking the wrong item or quantity, ultimately enhancing accuracy and customer satisfaction.
Track Picker Productivity
With direct visibility into the productivity of each picker, as well as their order accuracy, managers can easily see opportunities for training and team improvement, or to improve the staffing mix and help team members learn from one another.
How Pick-to-Light Picking System Works
Check out this real-life example of the VelocityPick™ system, built for zone picking—also known as “pick and pass.” Orders move through different zones until every item is picked.
Watch the video and follow our step-by-step guide to see how VelocityPick™ can speed up your picking process, boost accuracy, and help your e-comm store handle more SKUs without extra hassle for your team.
Batch & Zone Picking
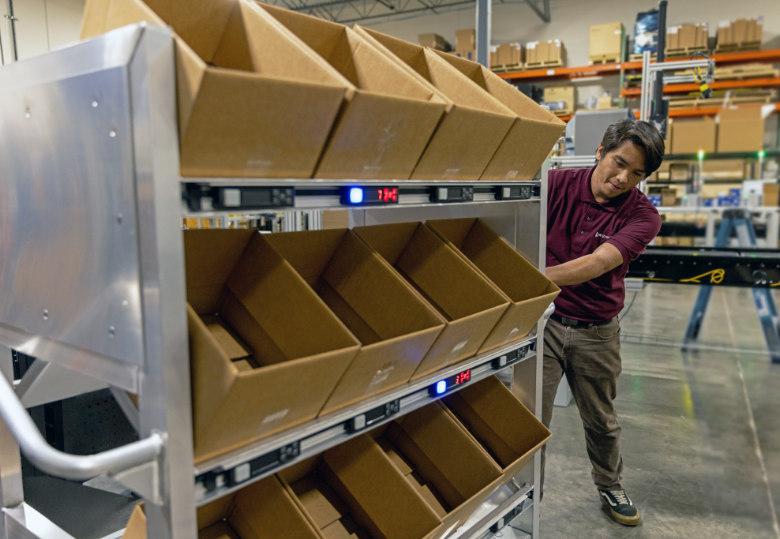
VelocityPick™ Smart Carts
Pickers can batch pick multiple order simultaneously using a pick-to-light equipped smart cart. The cart will be filled with empty cartons, each representing an order with its own ID.
The picker travels with the cart along either SKU-dense rack of common “high movers” until all order are fulfilled, or the cart may travel to the next “pick zone” where another worker takes the cart, until all orders are fulfilled. The rack can be active with lights, or passive with another marker such as a SKU or bin location.
VelocityPick™ Zone Pick
Each inventory bin location is equipped with a light module, usually along a consolidated inventory aisle, called a “forward pick rack”. Empty cartons convey to the pick-to-light area with their own unique ID barcode.
Once the carton is inducted, the system directs the picker to the location of the items by illuminating the corresponding lights. As each item is picked, the worker confirms the pick by pressing a button or triggering a sensor. Completed order cartons can advance once all items are picked.
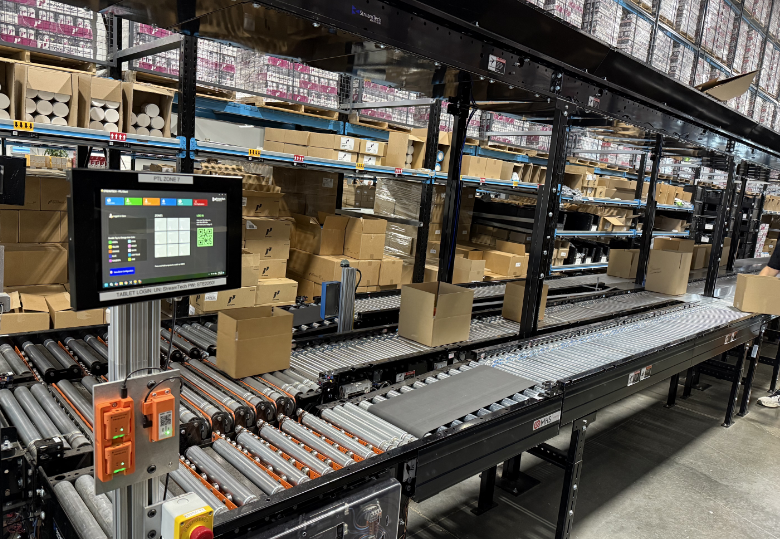
Put Wall Application
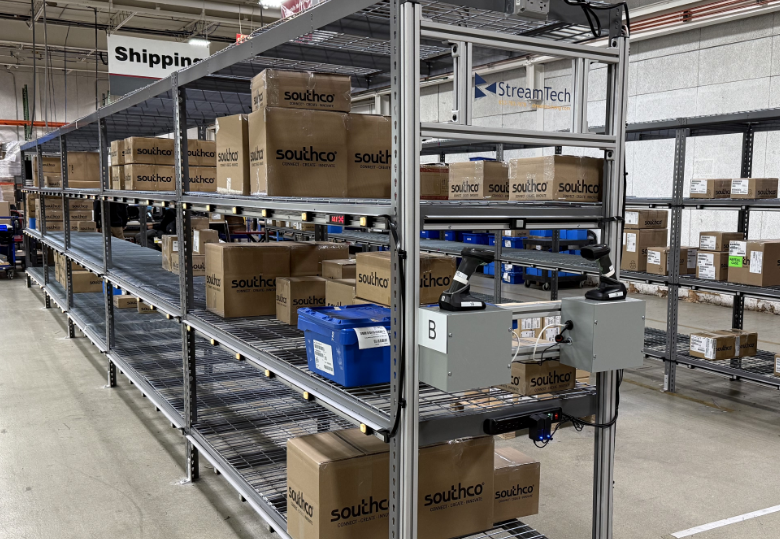
Use VelocityPick™ to Organize Your Orders
VelocityPick can be used as a Put Wall sorting system used to efficiently organize picked items for individual orders. Using pick-to-light button technology, each cubby in the wall lights up to indicate where specific items should be placed.
As items are scanned, the system guides workers to the correct bin with a light and quantity display, reducing errors and speeding up order fulfillment. Once all items for an order are placed, the bin lights up again to signal it’s ready for packing.
Server-Side Picking Software
StreamTech’s WCS Picking software interfaces with your WMS, and allows you to manage all the Picking Client stations, and gives you additional administrative functions such as:
- Manage operators’ accounts and log-ins
- Order import – wave and order management
- SKU management – importing form item master
- Bin/SKU mapping
- PTL device management – add/remove, monitor faults for PTL equipment
- Conveyor pick zone path routing
- See SKU quantities, lot numbers, picks per station
- See picks per minute
- Read and export weekly reports showing pick totals, average, scanner health and pick accuracy
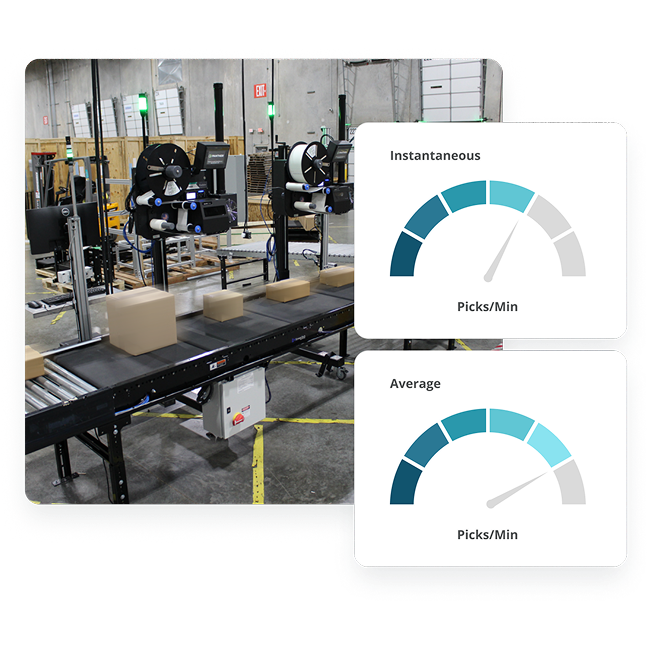
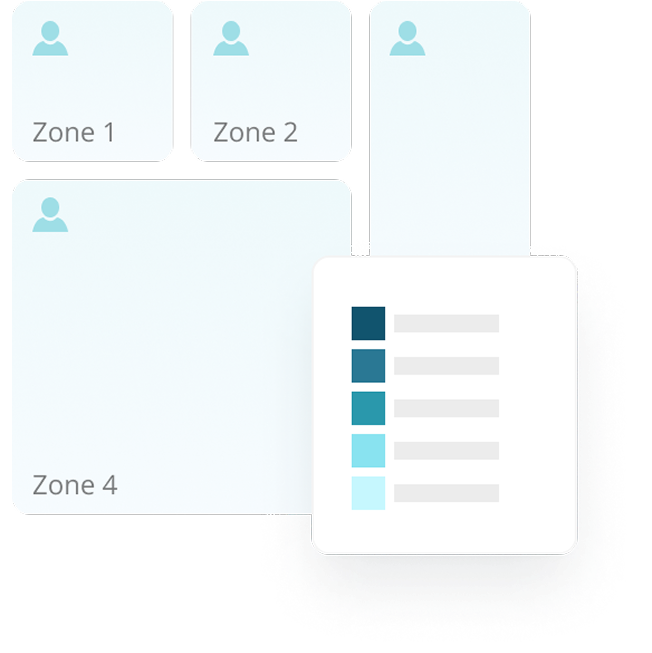
Client-Side Picking Software
On the client devices, picker operators can sign-in, and assign themselves to one or many pick zones. There is a client station at each zone for convenience.
- Sign-in by operator badge ID (tracks performance)
- Choose operator pick light colors
- Divide operators into full zones or split zones to up to 3 operators (called areas)
- Managers can use any client device to see the operator coverage of the whole system
What our customers say
Frequently Asked Questions
If you have any further questions, please reach out to us and we will be glad to help.
What is VelocityPick, and how does it work?
VelocityPick is a light-directed picking system that guides warehouse workers to the exact bin location and quantity for each SKU. As cartons travel down a conveyor, lights indicate which items to pick at each zone. Operators confirm each pick, and the carton moves to the next zone until the order is complete.
How does VelocityPick improve picking speed and accuracy?
By eliminating guesswork and reducing reliance on paper pick lists, VelocityPick boosts throughput by up to 60% and achieves up to 99% order accuracy. Light signals and scan confirmations minimize errors and help teams fulfill orders faster—even as SKU counts grow.
Can VelocityPick integrate with our WMS or ERP system?
Yes, VelocityPick integrates seamlessly with your existing WMS or ERP via StreamTech’s WCS software. It supports real-time updates, wave management, SKU mapping, and performance tracking to keep your operation running smoothly.
Is VelocityPick scalable for changing inventory or seasonal spikes?
Absolutely. VelocityPick modules and zones can be reconfigured or expanded to match evolving warehouse layouts, seasonal demand, or new product lines. It’s built to grow with your operation.
VelocityPick supports zone picking, pick-and-pass, and batch picking using smart carts. Each method helps streamline different warehouse layouts and order profiles while keeping labor efficient and easy to train.
Featured Articles
-
Technology
How Pick to Light Systems Increase Accuracy and Speed in Warehouse Operations
We know that dealing with shipping errors can feel like a never ending battle. It’s frustrating, time-consuming, and, frankly, a bit disheartening when the…
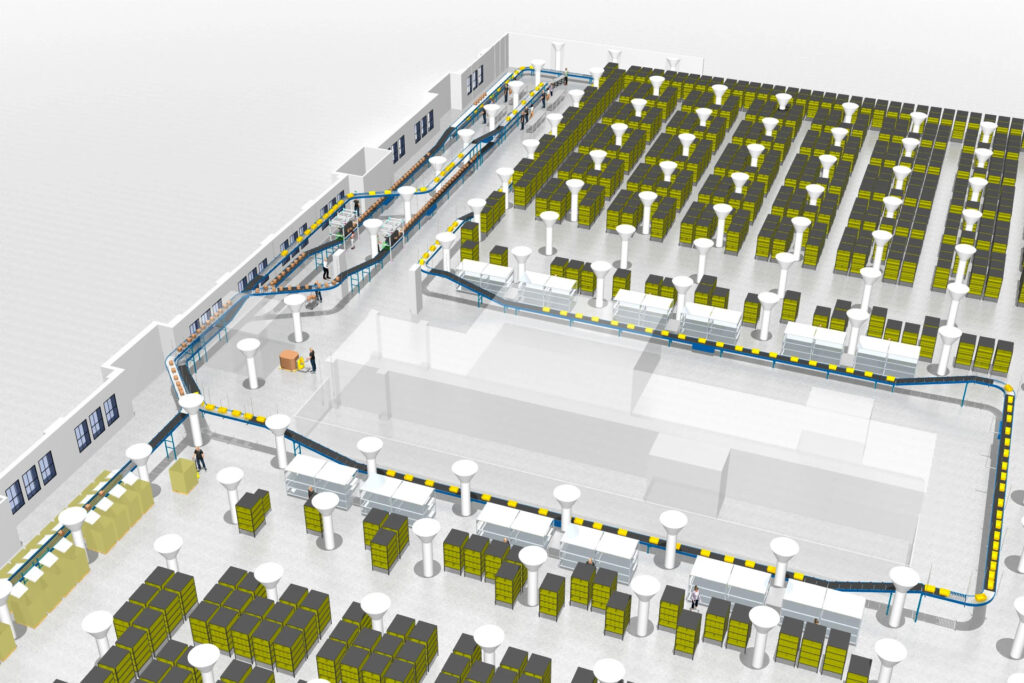
Ready for Automation?
Share your fulfillment challenge with us and we’ll design a custom solution for your business before you sign a contract
"*" indicates required fields