Auto Parts E-Retailer Brings Improvements to Culture, Customer Satisfaction
FCP Euro
FCP Euro, a leading online retailer of European car parts, implemented shipping automation to boost throughput, accuracy, and rate shopping efficiency. Instead of reducing headcount, the system elevated company culture by freeing fulfillment staff to move into new roles, all while enabling record Cyber Week sales with 400 more orders per hour and a stress-free operation.
Overview
FCP Euro (Foreign Car Parts) is a large online automotive parts retailer who specializes in European car parts, sourced and vetted from some of the highest quality manufacturers, with a lifetime warranty that is unbeatable in the industry. FCP Euro has cultivated a social following within the car enthusiast and racing communities, and hosts regular events in their Experience Center, where employees can even lift and work on their own car projects. In the past 10 years, FCP Euro has earned a spot on the Inc. 5000 fastest-growing private companies list eight times.
For FCP Euro, customer satisfaction is the primary driver for everything they do. The “customer-first” mindset has permeated across the company culture, so much so that many of their customers become employees. It’s for this reason they have a unique approach to implementing automation within their operations.
A Unique Approach
Instead of using automation as a labor reduction mechanism, FCP Euro took the approach that implementing automation could elevate their company culture by allowing many of the team members from the shipping and fulfillment team to move into new responsibilities within the company. For many of these employees, their roles now involve overseeing the automation, working on the customer engagement teams, or in the marketing department.
In addition to the team improvements, FCP Euro has other KPI’s to benchmark their success. They have seen a tremendous increase in throughput, order accuracy, and rate shopping efficiency. Instead of having 6 people manually dedicated to the rate shopping process, the StreamTech WCS software communicates with the shipping software and takes care of it automatically.
Additionally, during their biggest promotional season of the year, the annual Cyber Week sale, the team noticed a much more stress-free for the fulfillment and distribution environment, despite having the best sales results of any prior year, and processing an additional 400 more orders per hour than normal.
Solution Implementation
The shipping automation that FCP Euro has implemented had to fit into a relatively small space, due to the size of the existing facility in Connecticut, so it curves back on itself a few different times to allow the appropriate accumulation on the conveyor. The system starts at the 5 pack stations:
- Pack-Out: Packed orders are pushed through the semi-automatic tapers, adding the blue FCP Euro-branded tape on the top and bottom.
- Weigh, Dimension: Orders merge from the pack stations into the conveyor, and follow around to be inducted, weighed, and dimensioned in motion.
- Manifest & Rate Shop: Once the box has been identified and interrogated for weights, dimensions, the StreamTech Warehouse Control System (WCS) software interfaces with the customer’s shipping software to handle rate shopping by carrier and service level, and sends back the appropriate label.
- Print Apply: With two in-motion labelers, the system then labels each order. The dual labeling system allows for higher throughput during peak seasons.
- Exceptions And Palletization: Once labeled, orders make their way to the end of the line to be separated into pallets by carrier. There is a small exception lane where international orders go to be processed manually with the appropriate paperwork.
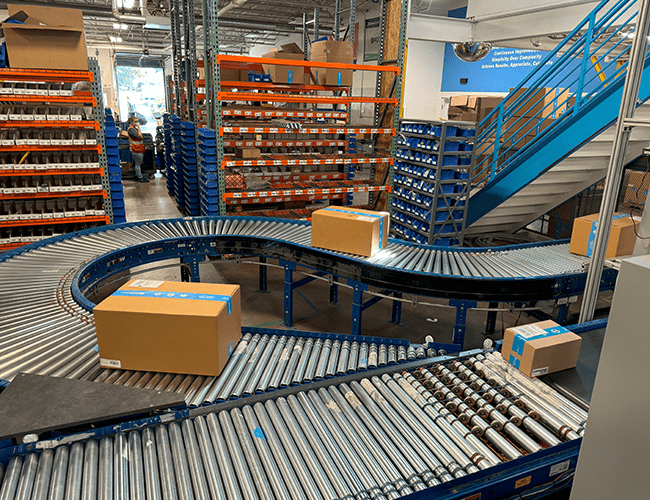
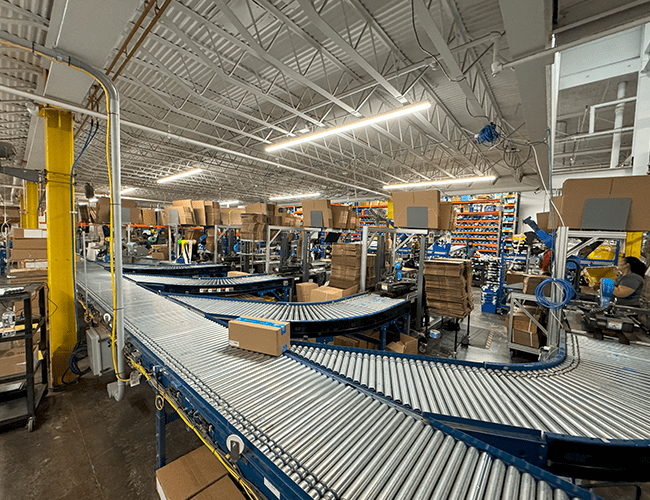
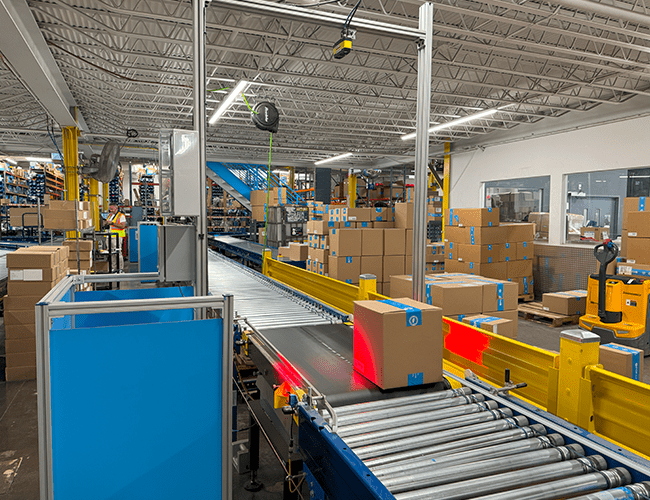
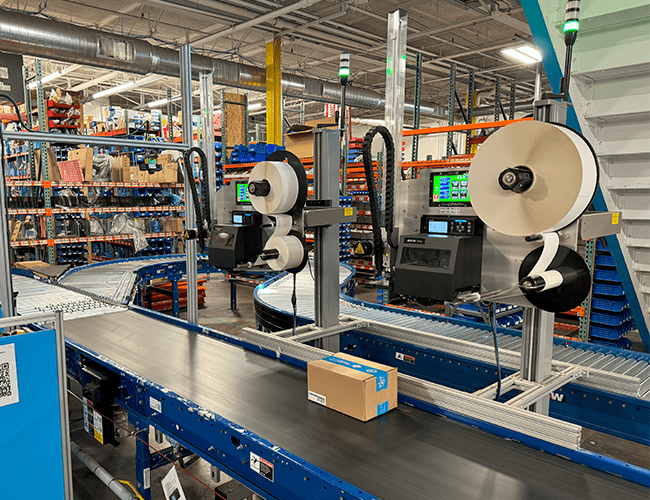
FCP Euro is an example of an organization that leads with customer satisfaction as the main driver of their business. This is reflected in FCP Euro’s long-term operational goal of delivering same day shipping to every state in the country. As the company continues to strive toward that goal, the StreamTech fulfillment automation is just one part of the story, and it is great to be involved in their continued success and growth.
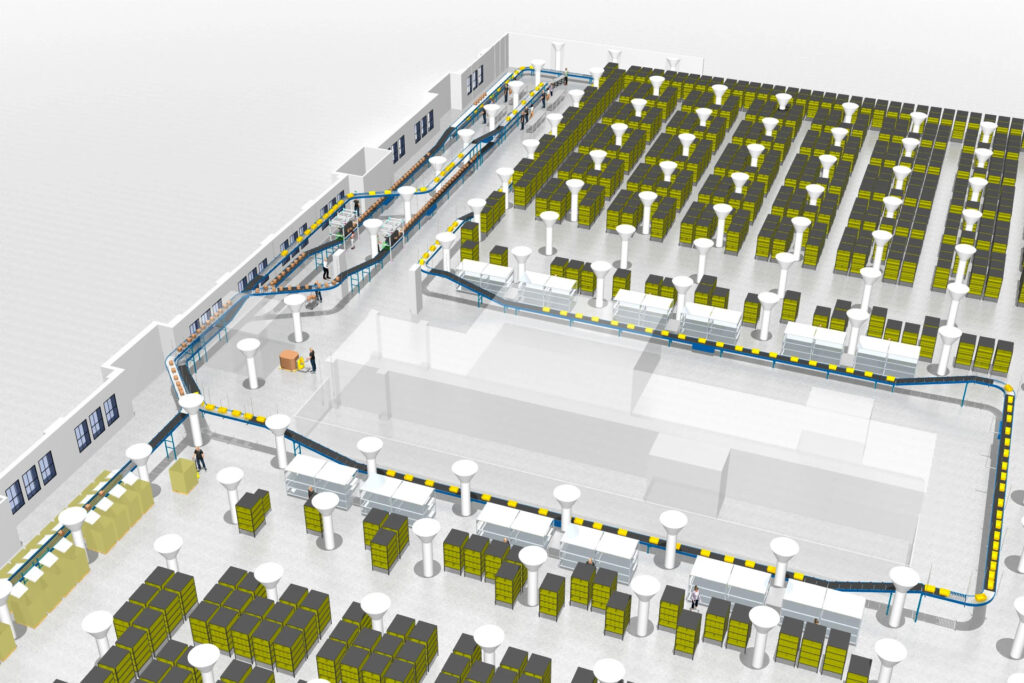
Ready for Automation?
Share your fulfillment challenge with us and we’ll design a custom solution for your business before you sign a contract
"*" indicates required fields