Why Is Automated Scanning So Important When Designing Fulfillment?
Why Is Automated Scanning So Important When Designing Fulfillment?
A little barcode consistency goes a long way toward your bottom line.
Why Is Automated Scanning So Important When Designing Fulfillment?
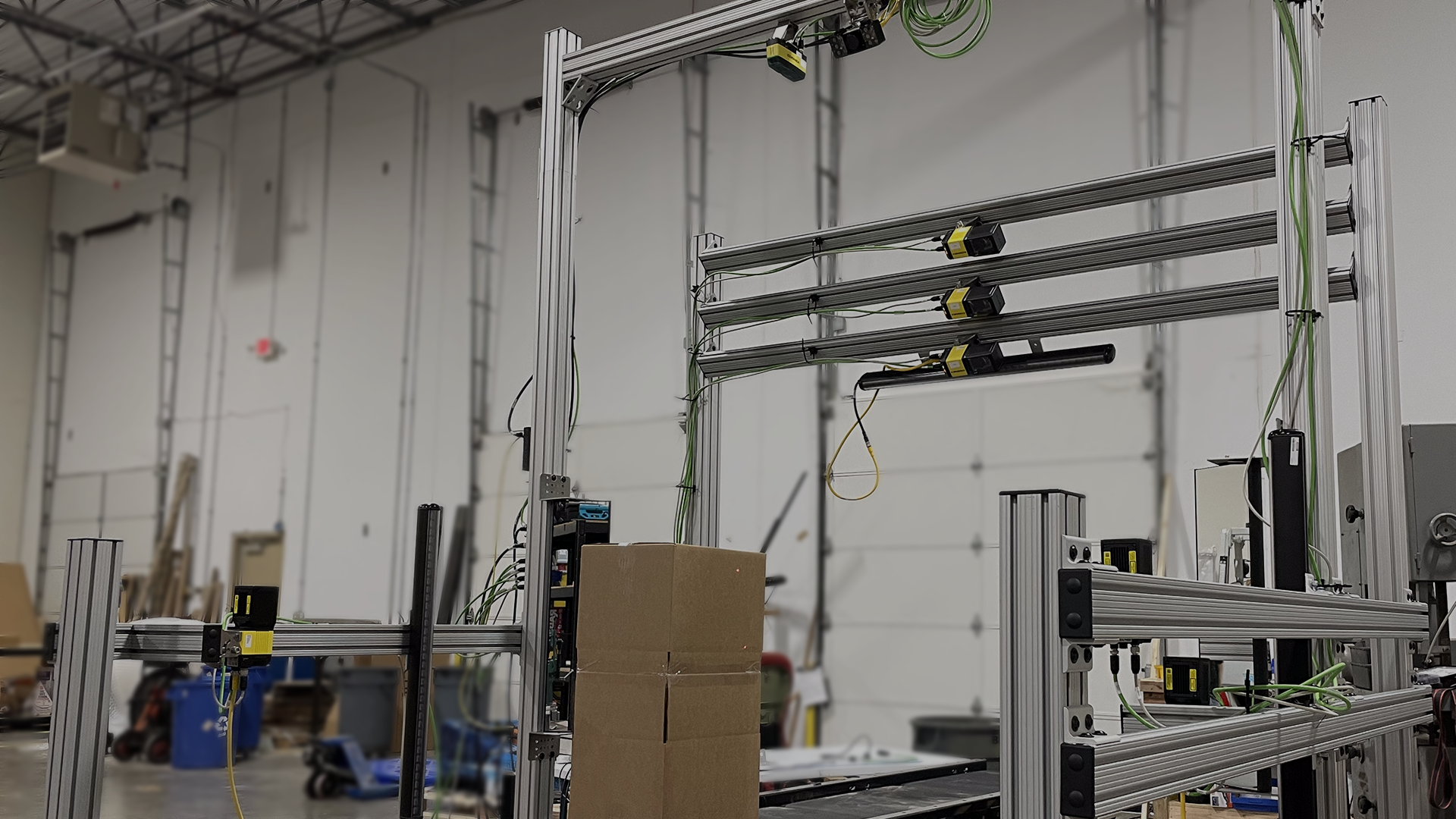
A little barcode consistency goes a long way toward your bottom line.
Introduction To Package Identification
For any successful fulfillment automation system to operate properly, the equipment must be able to uniquely identify each package. This identifier may be a License Plate (LPN) (for a pick-pack application — most common in fulfillment), it could be a Tracking Number (receiving applications), a Work Order (manufacturing), or a UPC (bulk shipping). Since a hand scanner is relatively inexpensive but fixed (automated scanning) can be somewhat tricky.
Barcodes may be 1D, or 2D: 1D codes have a series of variable width lines using symbologies like Code 128, Code 39, or UPC. 2D codes are made up of a checkerboard-like pattern. For example, a QR code is popular for scanning with a smartphone. Other 2D codes include Datamatrix and Maxicode. 2D codes can hold a lot of data so they are great for a weblink or even maintaining explicit information.
For pick-pack applications, we just need to essentially serialize the orders over a time-slice of perhaps a few days or weeks. Thus 6-9 digits is usually plenty of length and that’s what we’ll focus on for “License Plate” (LPN) applications.
Implications Of Label Placement
Understanding the purposes of the LPN and the types of barcodes used, we can dive into the details about why their placement is so important. Once that LPN barcode is read, the automation can begin to assign attributes to the order, such as weight and dimensions. This allows us to print and apply shipping labels accurately and ultimately report on the shipped status, sort location, and other data. We call this the “induct” scan.
Performing the induct scan requires the placement of a scanner along a side of the conveyor where the LPN will be located – typically to read the LPN on one side of the package. Consistent placement and alignment go a long way toward successful automation, saving you cost on unnecessary scanning equipment. Consistent LPN placement will reduce the number of scanners or cameras necessary to read a label.
In some cases, it could even allow you to reduce the number of redundant labelers. In a recent project, we were able to eliminate the need for a side-applied carrier label. The customer had requested a top-applied labeler and side-apply as well. However, we got creative – by instructing the operators to place LPNs on the front face of their packages, and induct packages on their side, we could use just one top-apply labeler, and accomplish both goals. A little bit of human cooperation goes a long way. The cost savings can be significant, and is only possible through cooperative owners and operators.
If the operator is unable to place the LPN in a consistent location, we add scanners to read each side, and each scanner adds to the equipment cost and programming complexity of the project.
(5-Sided Scan Tunnel on Left; 2-Sided Scan on Right)
Sure, We Can Do It; But Are You Sure You Want Us to?
Ultimately, if you are unable to control the placement of your LPN’s, or the orientation of your packages along the conveyor, our engineers can design systems that can read 5 (or even 6) sides of your packages, at any location. These are called scan tunnels, and involve about 10 specialized oscillating mirror scanners, as well as large fixed mirrors to ensure coverage across the entire package. It could theoretically even incorporate a between-roller scanner to capture labels on the bottom. The cost of a scan tunnel over the cost of traditional one-sided or two-sided scanning can be as much as a tenfold factor (or more), so it can be best to consider a compromise to bring consistency to the label placement, where practicable.
However, there are a variety of high-volume situations where many-sided automated scanning tunnels may be necessary. Situations where you are unable to control the location of the LPN, such as when utilizing only the manufacturer’s UPC label on the outside of the package. Some labeling applications utilize the WMS database and rely solely on the UPC.
Applications Where Multi-Sided Scanning may be necessary (generally in higher volume, very automated scanning facilities):
- Cross-Docking: scanning-in product UPCs straight from the dock door, from the manufacturer or supplier, weighing, dimensioning and labeling it straight for outbound carrier shipment, conveying to another outgoing dock, with no product storage.
- Inbound Receiving: scanning-in product UPCs or carrier labels straight from the carrier’s truck for inventory storage.
- Package Variation & Odd Shapes: in some instances, products are simply such a wide variety that a scan tunnel can be the most efficient way to account for all the variety. A combination of flats, bags, padded mailers, wide package size variety, and shrink-wrapped products could result in the need for a scan tunnel.
Often, the best way to meet the efficiency and ROI you are looking for is through some automation, combined with operator consistency as well. StreamTech’s applications engineers will work with you to define the scope of your project and provide recommendations about automated scanning for practical savings opportunities when possible.