Mason Companies, Inc. Consolidates Multiple Growing Fulfillment Operations Under One Roof
Mason Companies, Inc. Consolidates Multiple Growing Fulfillment Operations Under One Roof
Mason Companies, Inc.
Mason Companies, Inc. Consolidates Multiple Growing Fulfillment Operations Under One Roof
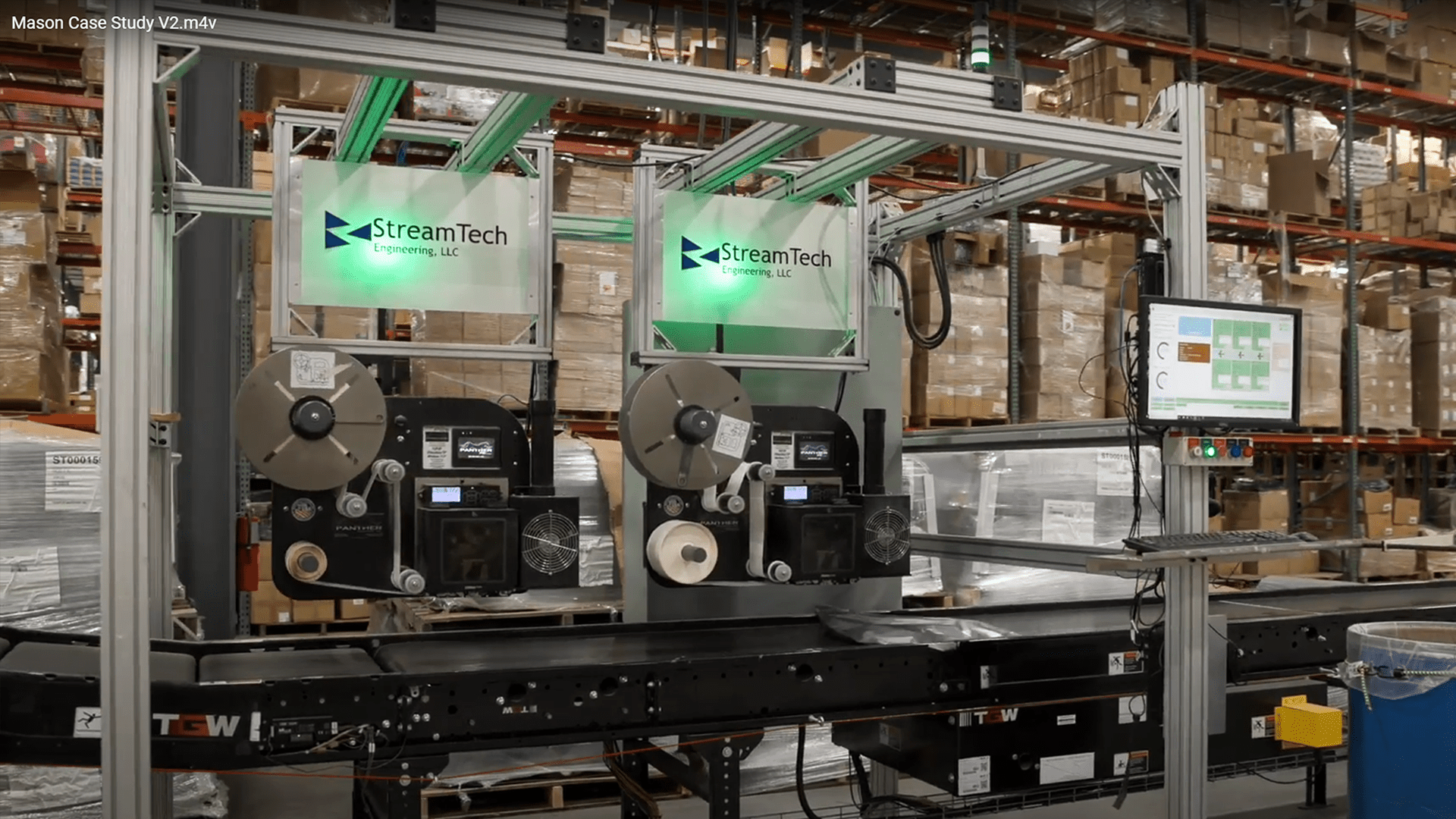
Mason Companies, Inc.
Growing, Diverse Product Offerings:
Mason’s continued growth initiatives and diverse product offerings required multiple fulfillment systems and packaging equipment. Now, Mason’s expansion has brought all their brands under one fulfillment and distribution center.
Mason Companies Inc. has a long history beginning as a shoe manufacturer in 1904, and has evolved its business model to include multiple catalogs and a diverse range of products. With a strong focus on customer satisfaction, Mason operates as a trusted retailer and distributor. Their extensive portfolio includes fashion apparel, footwear, home goods, and accessories, catering to individuals of all ages and styles.
With the high degree of variation in products, Mason has added new automation to accommodate each stage in their growth, over many years. StreamTech began working with Mason in 2007, and has provided many different systems for the company throughout the years, in different buildings. In 2021, Mason began working with StreamTech to implement a new system for one of their brands, as well as a proposal to consolidate the others under a new, much larger distribution and fulfillment center where all their fulfillment lines – for each brand – can sit under one roof.
The migration process was completed and the new system was implemented and running by Fall 2022. Today, Mason’s 425,000 square feet “MFC” (Mason Fulfillment Center) 425,000 square foot building fulfills between 25k to 60k items per day.
Three Fulfillment Automation Systems:
There are three main fulfillment lines at the Mason facility today, processing their various product lines:
- Bagged Items (30 per minute): primarily for clothing, the items flow from a bagger into the print-apply shipping system, and further to sortation, by carrier.
- Large Parcels (30 per minute): primarily for small household appliances, household items, and outdoor equipment; the items are processed as full cases, and are weighed, dimensioned, manifested and sorted.
- Mixed E-Commerce (30-40 per minute): this system integrates flow from fully automatic tapers and advanced fully automatic pack system, to in-motion weigh, dual print-apply, and sortation to multiple dock doors at the end of the line.
A Values-Driven Company:
Mason Companies Inc. upholds a set of core values that guide its operations and interactions with customers, employees, and stakeholders. Integrity serves as the foundation of their business practices, emphasizing honesty, transparency, and ethical conduct. They are committed to excellence, consistently delivering products and services of exceptional quality that surpass customer expectations.
Mason fosters a customer-centric approach, and values innovation to continuously seek new ideas, technologies, and strategies to stay ahead in a rapidly changing market. Diversity and inclusivity is another key value Mason embraces, fostering an environment that celebrates differences and promotes equality for their employees.
“Mason Companies is a very value-driven company, and there’s a lot of knowledge and teamwork involved in getting large projects such as this completed, and its great to work with a company that has the drive and the ambition to excel and do large projects like this, and come out successful.” Craig Ritzinger, Facilities Manager – Mason Companies
Mason Companies Inc. believes in giving back to the community and actively engages in initiatives to make a positive impact on society and the environment. These values will continue to drive Mason to develop new and innovative products, brands, and grow their company.
If you are considering new or existing automation upgrades, get in touch with a StreamTech team member and we look forward to discussing your project.