Experts in 3PL Fulfillment Automation Systems
Optimize Your Fulfillment Operations to Support Your Growing Client Base.
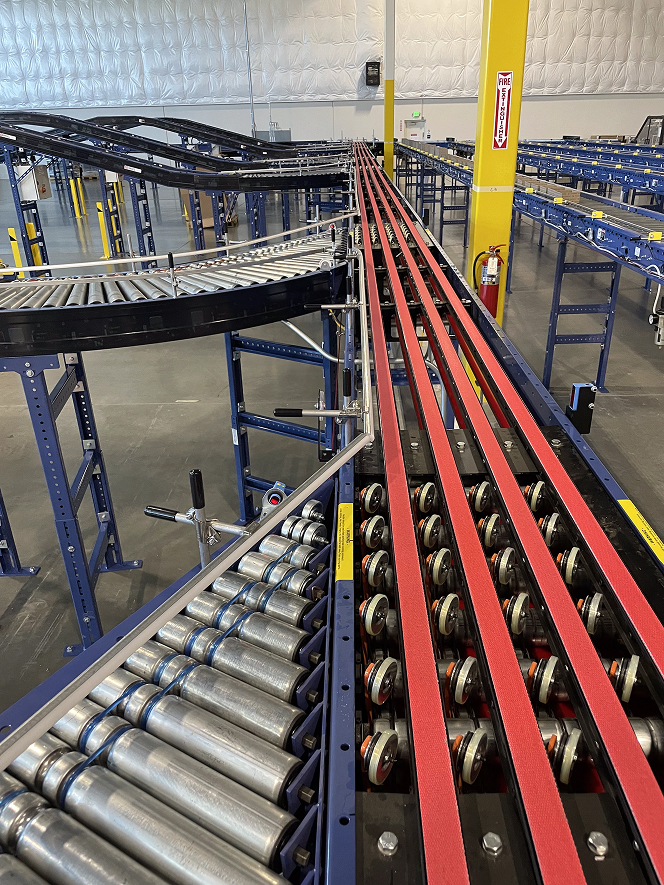
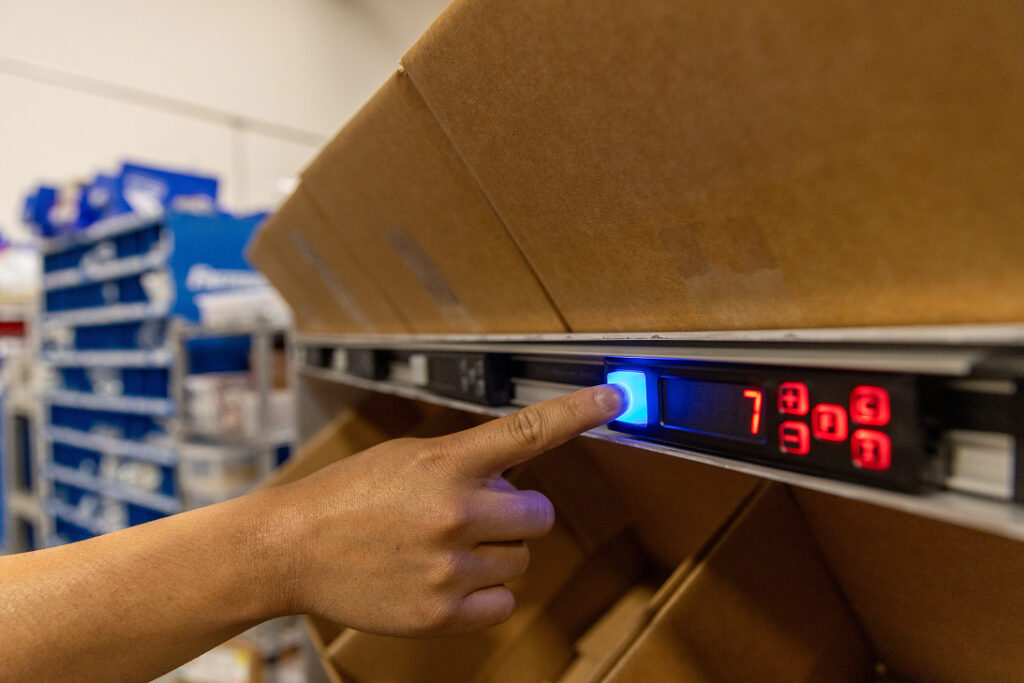
Crush Your SLAs with Smarter Fulfillment
Automating fulfillment allows 3PL providers to boost efficiency, cut labor and shipping costs, and consistently meet SLAs. With systems like conveyor lines, automated picking, packing, and sortation, 3PLs can process orders faster, reduce errors, and optimize inventory management. The result: streamlined operations, lower overhead, and smarter, more cost-effective shipping decisions that drive ROI and customer satisfaction.
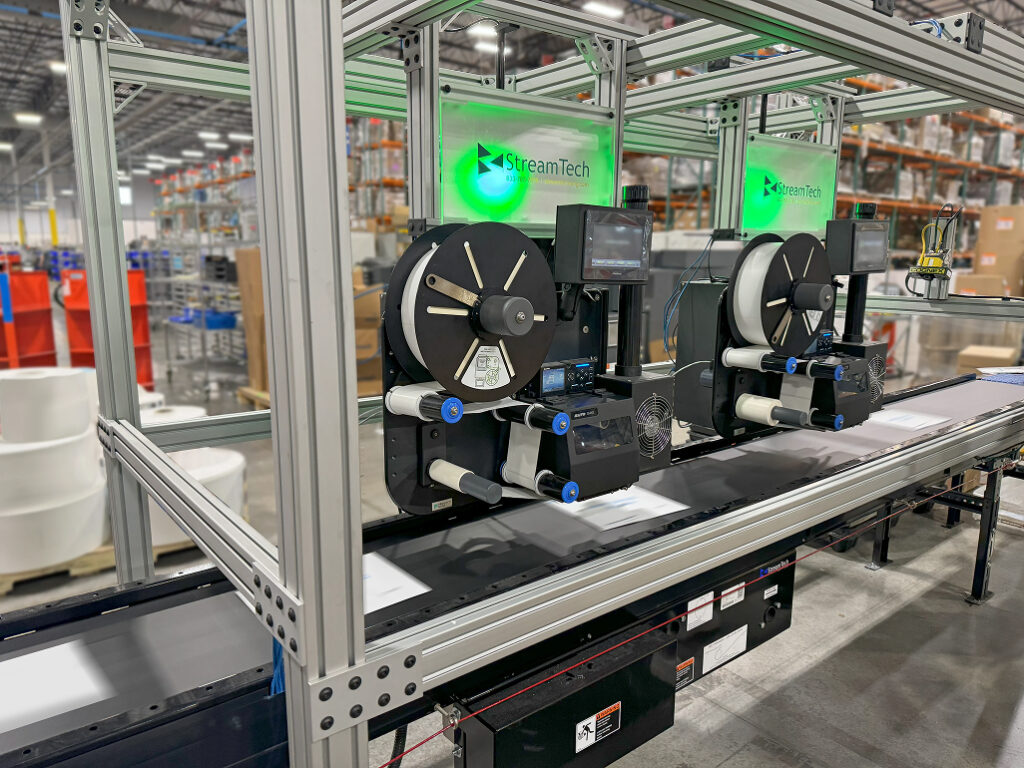
How Automated Fulfillment Powers 3PL Success
Software Integration Keeps You & Your Client Informed
StreamTech’s light WCS software handles orders as they are processed through your warehouse, integrating in real-time with your order database. This allows your software dashboards to accurately
report data back to your clients.
Easily Personalize Each Order for all the Brands You Fulfill For
Your customer may require unique packing slips, marketing cards or other custom gift messaging to be added to each order. These tasks can be automated into each order, unique to each client—without slowing down your operation.
Reduce Labor Strain & Fulfillment Costs
One of the top reasons that companies
look to automation is to reduce the strain on labor, for tasks such as picking, hand-applied labeling, and sorting orders. Manual workers can then be re-allocated to other value-added tasks.
Automate Pick & Pack for Processes for Efficiency
As the client base grows, so does the operational complexity. Using automated picking and packing processes ensures your labor is using the most effective route to complete the order. It also allows you to control dunnage and cartonization.
Increase Fulfillment Speed, While Lowering Shipping Costs
Automating the end-of-line shipping processes gives you a consistent operational speed, regardless of order flow. It also allows you to perform carrier and service-level rate shopping based on the most efficient prices, cutting costs.
Branded & Right-Sized Packaging Saves You Money
In addition to having a cost-effective shipping manifesting process, modern packaging equipment will design a box around each of your items. These systems can also add color branding to each box.
See How DCL Logistics
Uses Automation
During promotions, product launches, and peak demand, DCL’s order volume can double or triple. Adapting to these fluctuations is crucial for maintaining the high service levels clients expect. By leveraging automation, DCL scales seamlessly to ensure accurate, on-time, and cost-effective fulfillment—driving
customer satisfaction.
Your Smart Warehouse Starts Here
From pick to pack to parcel, we deliver fully automated warehouse solutions designed for third-party logistics. Eliminate manual bottlenecks, scale with confidence, and meet your clients’ SLAs with speed, accuracy, and reliability.
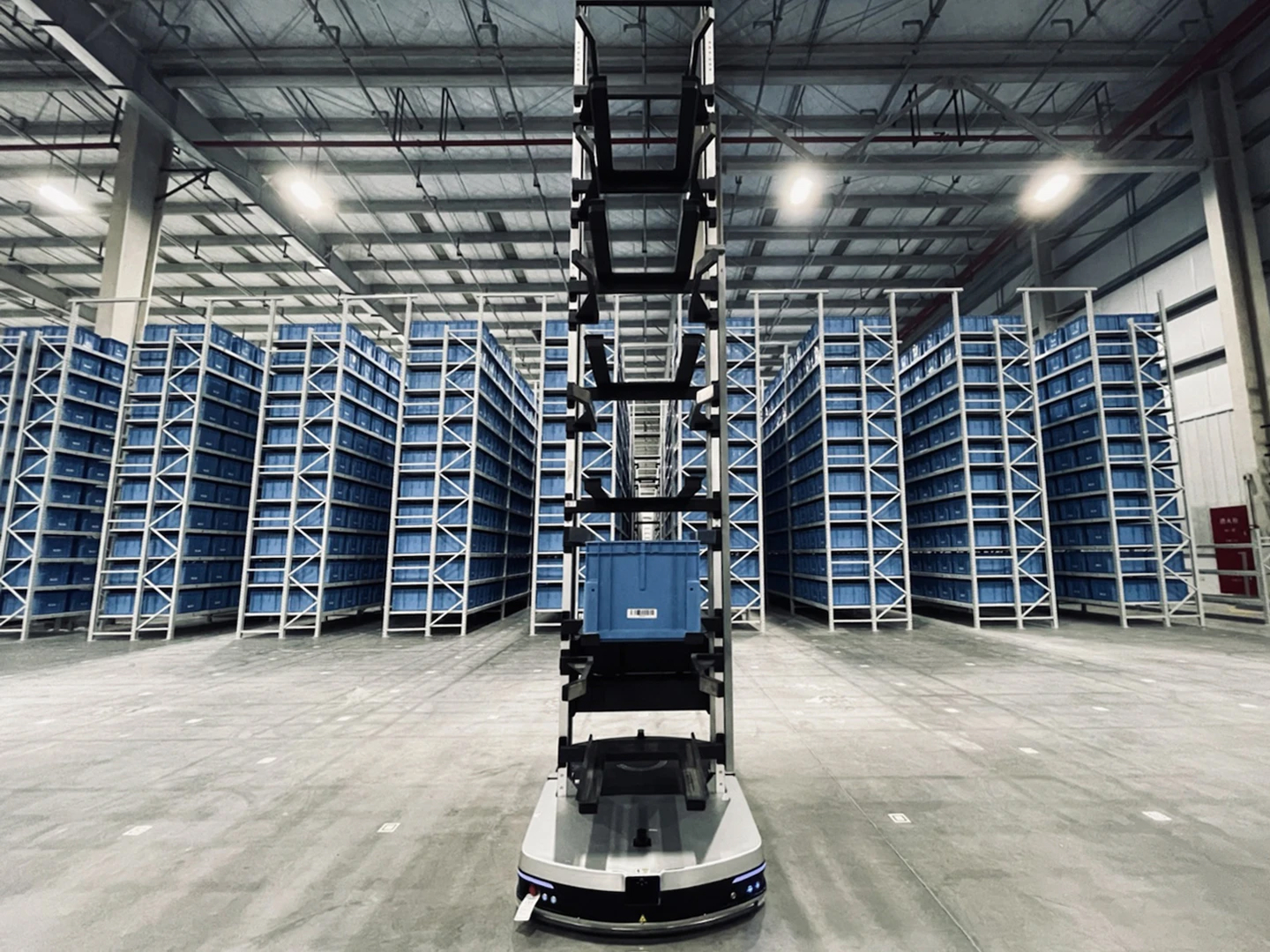
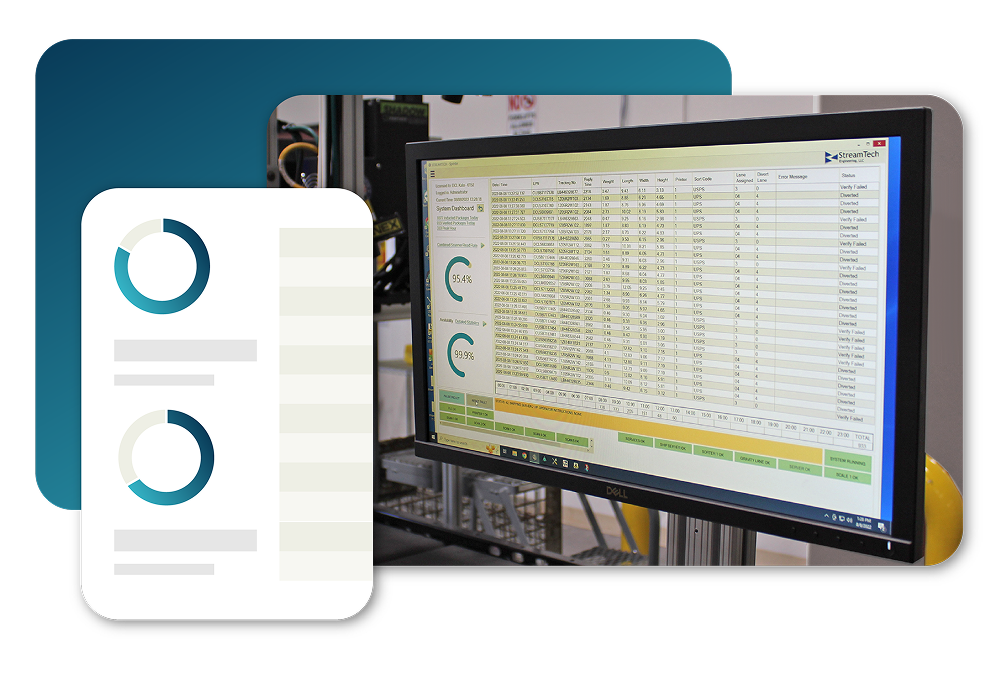
Software Integration Helps You Keep Your Clients Informed
Light WCS Software Delivers Real-Time Order Data
StreamTech’s WCS software handles orders as they are processed through your warehouse, and integrates seamlessly in real-time with your order databases. Allowing your existing software systems to handle inventory, manage orders, and share the data with you customers as you see fit.
Automate Dimensions, Weight and Shipping Labeling
Own Your Data—Let Your Software Handle Rate Shopping
With a full end-of-line shipping automation system, you can gather weights and dimensions in motion, rate shop them with your multi-carrier TMS software, and then put the right label on every package. These systems can operate starting at 15 CPM, and scale up easily from there.
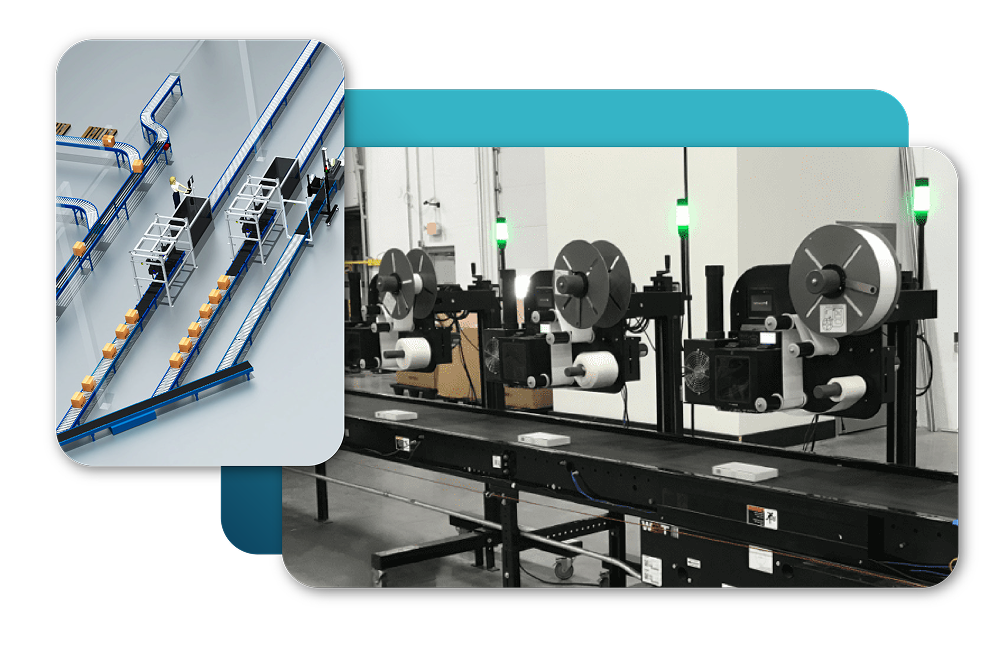
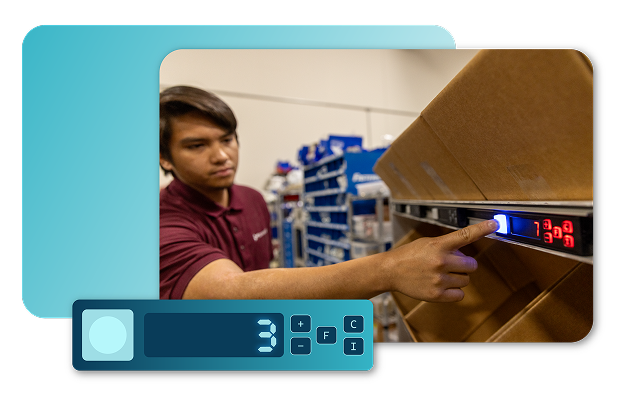
Increase Pick Accuracy & Speed
Reduce the amount of labor, training time, and errors in picking.
For 3PLs juggling high order volumes and diverse SKUs, Pick to Light streamlines fulfillment. It boosts pick speed, reduces errors, and simplifies training—helping you meet tight SLAs with confidence and consistency.
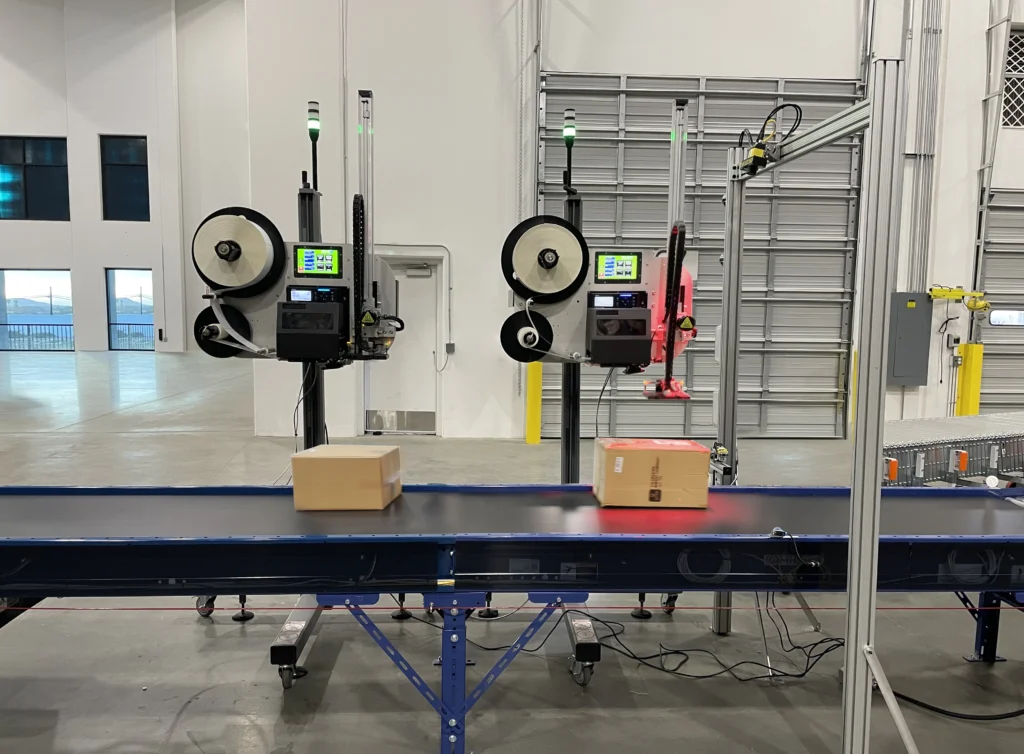
End-to-End Warehouse Fulfillment & Distribution Automation Solutions
We offer a suite of automation technologies designed to streamline your warehouse operations—from picking and packing to labeling and shipping. Our systems help you move and track products efficiently, reduce manual labor, and increase accuracy at every step of the fulfillment process.
Frequently Asked Questions
If you have any further questions, please reach out to us and we will be glad to help.
Can StreamTech’s systems support multiple client brands in one facility?
Yes. We specialize in building automation that’s flexible enough to support multi-client, multi-brand operations. Our systems can dynamically sort, label, and package orders according to the specific requirements of each brand—whether that’s custom packing slips, branded packaging, or routing rules—without disrupting overall throughput.
How does automation help us meet tight SLAs across multiple clients?
Speed and consistency are critical in 3PL. Our automation solutions—ranging from pick and pack systems to end-of-line shipping sorters—accelerate order processing while reducing errors. With fewer manual touches and faster cycle times, you’ll be in a stronger position to meet or exceed SLAs across all your client accounts.
What if our fulfillment volume fluctuates throughout the year?
No problem. We design scalable systems that can flex with your business. Whether you’re dealing with seasonal spikes, onboarding new clients, or managing daily variability, our solutions are built to handle surges without compromising speed or accuracy.
Can your systems integrate with our existing WMS or OMS?
In most cases, yes. Our software integrates with a wide range of warehouse and order management platforms. We’ll work closely with your team to ensure seamless communication between systems, so you and your clients always have access to real-time, accurate data.
What kind of support does StreamTech offer after installation?
We don’t disappear after install. We provide ongoing support, including remote diagnostics, preventative maintenance, software updates, and fast access to replacement parts. You’ll have a dedicated team to help you troubleshoot issues and keep your systems running at peak performance.
Featured Articles
-
Best Practices
Why the Best Material Handling Solutions Begin with the Right Questions
In today’s high-pressure fulfillment world, it’s tempting to “just get a quote” and keep things moving. But when it comes to automation, fast answers…
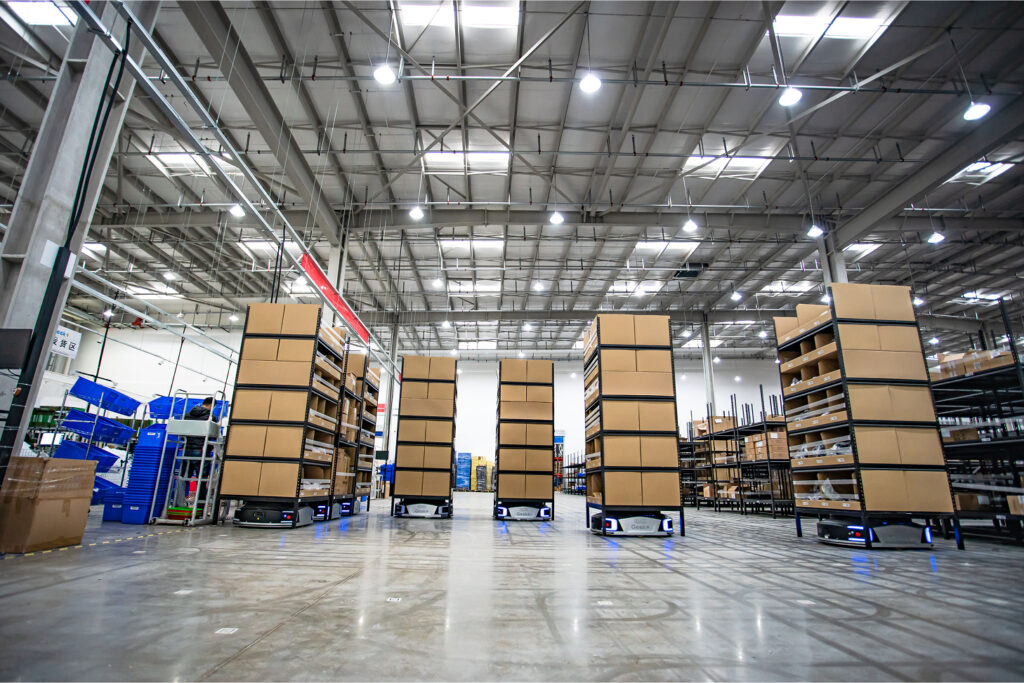
Ready for Automation?
Share your fulfillment challenge with us and we’ll design a custom solution for your business before you sign a contract
"*" indicates required fields